ເທກໂນໂລຍີ dicing wafer, ເປັນບາດກ້າວທີ່ສໍາຄັນໃນຂະບວນການຜະລິດ semiconductor, ແມ່ນເຊື່ອມຕໍ່ໂດຍກົງກັບການປະຕິບັດຊິບ, ຜົນຜະລິດ, ແລະຄ່າໃຊ້ຈ່າຍໃນການຜະລິດ.
#01 ຄວາມເປັນມາແລະຄວາມສໍາຄັນຂອງ Wafer Dicing
1.1 ຄໍານິຍາມຂອງ Wafer Dicing
Wafer dicing (ຊຶ່ງເອີ້ນກັນວ່າ scribing) ແມ່ນຂັ້ນຕອນທີ່ສໍາຄັນໃນການຜະລິດ semiconductor, ມີຈຸດປະສົງເພື່ອແບ່ງ wafers ປຸງແຕ່ງເຂົ້າໄປໃນຫຼາຍໆຄົນ. ຕາຍເຫຼົ່ານີ້ໂດຍປົກກະຕິປະກອບດ້ວຍການທໍາງານຂອງວົງຈອນທີ່ສົມບູນແລະເປັນອົງປະກອບຫຼັກທີ່ໃຊ້ໃນການຜະລິດອຸປະກອນເອເລັກໂຕຣນິກໃນທີ່ສຸດ. ໃນຂະນະທີ່ການອອກແບບຊິບກາຍເປັນສະລັບສັບຊ້ອນຫຼາຍແລະຂະຫນາດຍັງສືບຕໍ່ຫຼຸດລົງ, ຄວາມຕ້ອງການຄວາມແມ່ນຍໍາແລະປະສິດທິພາບສໍາລັບເທກໂນໂລຍີ dicing wafer ແມ່ນເຂັ້ມງວດຫຼາຍຂຶ້ນ.
ໃນການປະຕິບັດຕົວຈິງ, wafer dicing ປົກກະຕິແລ້ວໃຊ້ເຄື່ອງມືທີ່ມີຄວາມແມ່ນຍໍາສູງເຊັ່ນ: ແຜ່ນໃບຄ້າຍຄືເພັດເພື່ອຮັບປະກັນວ່າການຕາຍແຕ່ລະຄົນຍັງຄົງ intact ແລະເຮັດວຽກຢ່າງເຕັມທີ່. ຂັ້ນຕອນທີ່ສໍາຄັນປະກອບມີການກະກຽມກ່ອນການຕັດ, ການຄວບຄຸມທີ່ຊັດເຈນໃນລະຫວ່າງຂະບວນການຕັດ, ແລະການກວດກາຄຸນນະພາບຫຼັງຈາກການຕັດ.
ກ່ອນທີ່ຈະຕັດ, wafer ຕ້ອງໄດ້ຮັບການຫມາຍແລະຕໍາແຫນ່ງເພື່ອຮັບປະກັນເສັ້ນທາງຕັດທີ່ຖືກຕ້ອງ. ໃນລະຫວ່າງການຕັດ, ຕົວກໍານົດການເຊັ່ນຄວາມກົດດັນຂອງເຄື່ອງມືແລະຄວາມໄວຕ້ອງໄດ້ຮັບການຄວບຄຸມຢ່າງເຂັ້ມງວດເພື່ອປ້ອງກັນຄວາມເສຍຫາຍຂອງ wafer. ຫຼັງຈາກການຕັດ, ການກວດກາຄຸນນະພາບທີ່ສົມບູນແບບແມ່ນດໍາເນີນເພື່ອຮັບປະກັນວ່າທຸກໆຊິບຕອບສະຫນອງມາດຕະຖານການປະຕິບັດ.
ຫຼັກການພື້ນຖານຂອງເທກໂນໂລຍີ dicing wafer ກວມເອົາບໍ່ພຽງແຕ່ການຄັດເລືອກອຸປະກອນການຕັດແລະການກໍານົດຕົວກໍານົດການຂອງຂະບວນການ, ແຕ່ຍັງອິດທິພົນຂອງຄຸນສົມບັດກົນຈັກແລະຄຸນລັກສະນະຂອງວັດສະດຸກ່ຽວກັບຄຸນນະພາບການຕັດ. ສໍາລັບຕົວຢ່າງ, wafers ຊິລິໂຄນ dielectric ຕ່ໍາ k, ເນື່ອງຈາກຄຸນສົມບັດກົນຈັກ inferior ຂອງເຂົາເຈົ້າ, ມີຄວາມອ່ອນໄຫວສູງຕໍ່ຄວາມເຂັ້ມຂົ້ນຂອງຄວາມກົດດັນໃນລະຫວ່າງການຕັດ, ນໍາໄປສູ່ຄວາມລົ້ມເຫຼວເຊັ່ນ chipping ແລະ cracking. ຄວາມແຂງແລະ brittleness ຕ່ໍາຂອງວັດສະດຸ k ຕ່ໍາເຮັດໃຫ້ພວກເຂົາມີຄວາມສ່ຽງຕໍ່ຄວາມເສຍຫາຍຂອງໂຄງສ້າງພາຍໃຕ້ການບັງຄັບກົນຈັກຫຼືຄວາມກົດດັນຄວາມຮ້ອນ, ໂດຍສະເພາະໃນໄລຍະການຕັດ. ການຕິດຕໍ່ລະຫວ່າງເຄື່ອງມືແລະຫນ້າດິນ wafer, ບວກໃສ່ກັບອຸນຫະພູມສູງ, ສາມາດເຮັດໃຫ້ຄວາມເຂັ້ມຂົ້ນຂອງຄວາມກົດດັນຮ້າຍແຮງຂຶ້ນ.
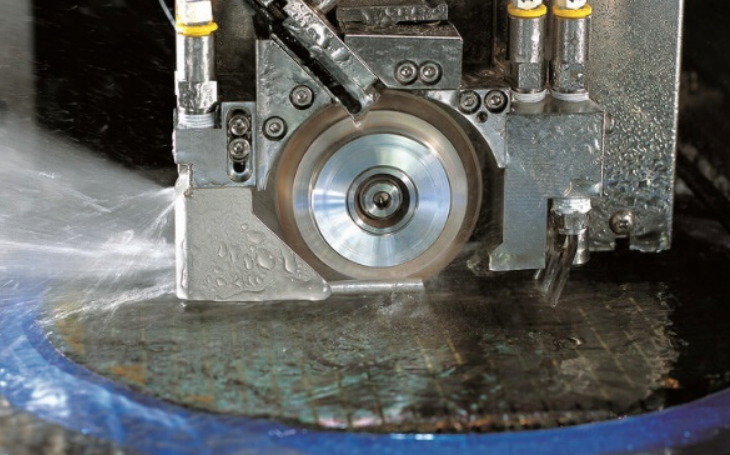
ດ້ວຍຄວາມກ້າວຫນ້າທາງດ້ານວິທະຍາສາດວັດສະດຸ, ເທກໂນໂລຍີ dicing wafer ໄດ້ຂະຫຍາຍອອກໄປນອກເຫນືອເຄື່ອງ semiconductors ທີ່ໃຊ້ຊິລິຄອນແບບດັ້ງເດີມເພື່ອປະກອບມີວັດສະດຸໃຫມ່ເຊັ່ນ gallium nitride (GaN). ວັດສະດຸໃຫມ່ເຫຼົ່ານີ້, ເນື່ອງຈາກຄວາມແຂງກະດ້າງແລະຄຸນສົມບັດຂອງໂຄງສ້າງ, ເຮັດໃຫ້ເກີດສິ່ງທ້າທາຍໃຫມ່ສໍາລັບຂະບວນການ dicing, ຮຽກຮ້ອງໃຫ້ມີການປັບປຸງເພີ່ມເຕີມໃນເຄື່ອງມືຕັດແລະເຕັກນິກ.
ໃນຖານະເປັນຂະບວນການທີ່ສໍາຄັນໃນອຸດສາຫະກໍາ semiconductor, dicing wafer ສືບຕໍ່ໄດ້ຮັບການປັບປຸງໃຫ້ດີທີ່ສຸດເພື່ອຕອບສະຫນອງຄວາມຕ້ອງການຂອງການພັດທະນາແລະຄວາມກ້າວຫນ້າທາງດ້ານເຕັກໂນໂລຢີ, ວາງພື້ນຖານສໍາລັບ microelectronics ແລະເຕັກໂນໂລຢີວົງຈອນປະສົມປະສານໃນອະນາຄົດ.
ການປັບປຸງເຕັກໂນໂລຊີ wafer dicing ໄປນອກເຫນືອການພັດທະນາອຸປະກອນການແລະເຄື່ອງມື. ພວກເຂົາເຈົ້າຍັງກວມເອົາການເພີ່ມປະສິດທິພາບຂະບວນການ, ການປັບປຸງປະສິດທິພາບຂອງອຸປະກອນ, ແລະການຄວບຄຸມທີ່ຊັດເຈນຂອງຕົວກໍານົດການ dicing. ຄວາມກ້າວຫນ້າເຫຼົ່ານີ້ມີຈຸດປະສົງເພື່ອຮັບປະກັນຄວາມແມ່ນຍໍາສູງ, ປະສິດທິພາບ, ແລະຄວາມຫມັ້ນຄົງໃນຂະບວນການ wafer dicing, ຕອບສະຫນອງຄວາມຕ້ອງການຂອງອຸດສາຫະກໍາ semiconductor ສໍາລັບຂະຫນາດຂະຫນາດນ້ອຍ, ການເຊື່ອມໂຍງທີ່ສູງຂຶ້ນ, ແລະໂຄງສ້າງ chip ສະລັບສັບຊ້ອນຫຼາຍ.
ເຂດການປັບປຸງ | ມາດຕະການສະເພາະ | ຜົນກະທົບ |
ການເພີ່ມປະສິດທິພາບຂະບວນການ | - ປັບປຸງການກະກຽມເບື້ອງຕົ້ນເຊັ່ນ: ການຈັດວາງ wafer ທີ່ຖືກຕ້ອງຫຼາຍຂຶ້ນ ແລະ ການວາງແຜນເສັ້ນທາງ. | - ຫຼຸດຜ່ອນຄວາມຜິດພາດຂອງການຕັດແລະປັບປຸງຄວາມຫມັ້ນຄົງ. |
- ຫຼຸດຜ່ອນຄວາມຜິດພາດຂອງການຕັດແລະເພີ່ມຄວາມຫມັ້ນຄົງ. | - ນຳໃຊ້ກົນໄກການຕິດຕາມ ແລະ ຕອບສະໜອງແບບສົດໆເພື່ອປັບຄວາມດັນ, ຄວາມໄວ ແລະ ອຸນຫະພູມຂອງເຄື່ອງມື. | |
- ອັດຕາການແຕກຫັກຂອງ wafer ຕ່ໍາແລະປັບປຸງຄຸນນະພາບຂອງຊິບ. | ||
ການເພີ່ມປະສິດທິພາບຂອງອຸປະກອນ | - ນໍາໃຊ້ລະບົບກົນຈັກທີ່ມີຄວາມແມ່ນຍໍາສູງແລະເຕັກໂນໂລຊີການຄວບຄຸມອັດຕະໂນມັດກ້າວຫນ້າ. | - ປັບປຸງຄວາມຖືກຕ້ອງຂອງການຕັດແລະຫຼຸດຜ່ອນການສູນເສຍວັດສະດຸ. |
- ແນະນໍາເຕັກໂນໂລຊີການຕັດ laser ທີ່ເຫມາະສົມສໍາລັບ wafers ວັດສະດຸແຂງສູງ. | - ປັບປຸງປະສິດທິພາບການຜະລິດແລະຫຼຸດຜ່ອນຄວາມຜິດພາດຄູ່ມື. | |
- ເພີ່ມທະວີການອັດຕະໂນມັດອຸປະກອນສໍາລັບການຕິດຕາມກວດກາອັດຕະໂນມັດແລະການປັບ. | ||
ການຄວບຄຸມພາລາມິເຕີທີ່ຊັດເຈນ | - ປັບຕົວກໍານົດການເຊັ່ນ: ຄວາມເລິກຕັດ, ຄວາມໄວ, ປະເພດເຄື່ອງມື, ແລະວິທີການເຮັດຄວາມເຢັນ. | - ຮັບປະກັນຄວາມສົມບູນຕາຍ ແລະປະສິດທິພາບໄຟຟ້າ. |
- ປັບຕົວກໍານົດການໂດຍອີງໃສ່ວັດສະດຸ wafer, ຄວາມຫນາ, ແລະໂຄງສ້າງ. | - ຊຸກຍູ້ອັດຕາຜົນຜະລິດ, ຫຼຸດຜ່ອນສິ່ງເສດເຫຼືອຂອງວັດສະດຸ, ແລະຕົ້ນທຶນການຜະລິດຕ່ໍາ. | |
ຄວາມສໍາຄັນຍຸດທະສາດ | - ສືບຕໍ່ຄົ້ນຫາເສັ້ນທາງເຕັກໂນໂລຊີໃຫມ່, ປັບປຸງຂະບວນການ, ແລະເສີມຂະຫຍາຍຄວາມສາມາດຂອງອຸປະກອນເພື່ອຕອບສະຫນອງຄວາມຕ້ອງການຂອງຕະຫຼາດ. | - ປັບປຸງຜົນຜະລິດແລະປະສິດທິພາບການຜະລິດຊິບ, ສະຫນັບສະຫນູນການພັດທະນາວັດສະດຸໃຫມ່ແລະການອອກແບບຊິບກ້າວຫນ້າ. |
1.2 ຄວາມສໍາຄັນຂອງ Wafer Dicing
Wafer dicing ມີບົດບາດສໍາຄັນໃນຂະບວນການຜະລິດ semiconductor, ມີຜົນກະທົບໂດຍກົງຕໍ່ຂັ້ນຕອນຕໍ່ໄປເຊັ່ນດຽວກັນກັບຄຸນນະພາບແລະການປະຕິບັດຂອງຜະລິດຕະພັນສຸດທ້າຍ. ຄວາມສໍາຄັນຂອງມັນສາມາດມີລາຍລະອຽດດັ່ງຕໍ່ໄປນີ້:
ຫນ້າທໍາອິດ, ຄວາມຖືກຕ້ອງແລະຄວາມສອດຄ່ອງຂອງ dicing ແມ່ນກຸນແຈເພື່ອໃຫ້ແນ່ໃຈວ່າຜົນຜະລິດຂອງຊິບແລະຄວາມຫນ້າເຊື່ອຖື. ໃນລະຫວ່າງການຜະລິດ, wafers ດໍາເນີນການຫຼາຍຂັ້ນຕອນເພື່ອປະກອບເປັນໂຄງສ້າງວົງຈອນ intricate ຈໍານວນຫລາຍ, ເຊິ່ງຈະຕ້ອງໄດ້ແບ່ງອອກຢ່າງຊັດເຈນເປັນ chip ບຸກຄົນ (ຕາຍ). ຖ້າມີຄວາມຜິດພາດທີ່ສໍາຄັນໃນການຈັດຕໍາແຫນ່ງຫຼືການຕັດໃນລະຫວ່າງການຂະບວນການ dicing, ວົງຈອນອາດຈະໄດ້ຮັບຄວາມເສຍຫາຍ, ຜົນກະທົບຕໍ່ການເຮັດວຽກແລະຄວາມຫນ້າເຊື່ອຖືຂອງ chip ໄດ້. ດັ່ງນັ້ນ, ເທກໂນໂລຍີ dicing ທີ່ມີຄວາມແມ່ນຍໍາສູງບໍ່ພຽງແຕ່ຮັບປະກັນຄວາມສົມບູນຂອງແຕ່ລະຊິບ, ແຕ່ຍັງປ້ອງກັນຄວາມເສຍຫາຍຂອງວົງຈອນພາຍໃນ, ປັບປຸງອັດຕາຜົນຜະລິດໂດຍລວມ.
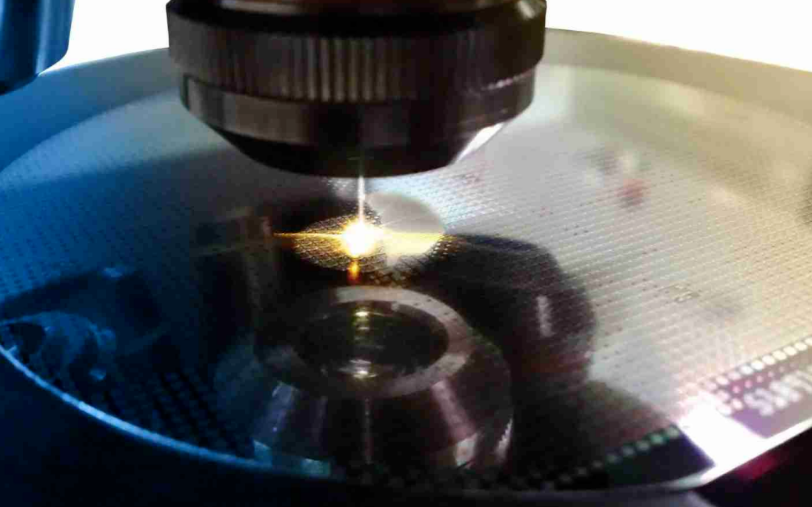
ອັນທີສອງ, dicing wafer ມີຜົນກະທົບຢ່າງຫຼວງຫຼາຍຕໍ່ປະສິດທິພາບການຜະລິດແລະການຄວບຄຸມຄ່າໃຊ້ຈ່າຍ. ເປັນຂັ້ນຕອນສໍາຄັນໃນຂະບວນການຜະລິດ, ປະສິດທິພາບຂອງມັນມີຜົນກະທົບໂດຍກົງຕໍ່ຄວາມກ້າວຫນ້າຂອງຂັ້ນຕອນຕໍ່ໄປ. ໂດຍການເພີ່ມປະສິດທິພາບຂອງຂະບວນການ dicing, ເພີ່ມລະດັບອັດຕະໂນມັດ, ແລະການປັບປຸງຄວາມໄວຂອງການຕັດ, ປະສິດທິພາບການຜະລິດໂດຍລວມສາມາດປັບປຸງຢ່າງຫຼວງຫຼາຍ.
ໃນທາງກົງກັນຂ້າມ, ການສູນເສຍວັດສະດຸໃນລະຫວ່າງການ dicing ແມ່ນປັດໃຈສໍາຄັນໃນການຄຸ້ມຄອງຄ່າໃຊ້ຈ່າຍ. ການນໍາໃຊ້ເຕັກໂນໂລຊີ dicing ກ້າວຫນ້າທາງດ້ານບໍ່ພຽງແຕ່ຫຼຸດຜ່ອນການສູນເສຍວັດສະດຸທີ່ບໍ່ຈໍາເປັນໃນລະຫວ່າງການຂະບວນການຕັດ, ແຕ່ຍັງເພີ່ມການນໍາໃຊ້ wafer, ດັ່ງນັ້ນການຫຼຸດລົງຄ່າໃຊ້ຈ່າຍໃນການຜະລິດ.
ດ້ວຍຄວາມກ້າວຫນ້າຂອງເທກໂນໂລຍີ semiconductor, ເສັ້ນຜ່າສູນກາງຂອງ wafer ຍັງສືບຕໍ່ເພີ່ມຂຶ້ນ, ແລະຄວາມຫນາແຫນ້ນຂອງວົງຈອນເພີ່ມຂຶ້ນຕາມຄວາມເຫມາະສົມ, ຄວາມຕ້ອງການທີ່ສູງຂຶ້ນໃນເຕັກໂນໂລຢີ dicing. wafers ຂະຫນາດໃຫຍ່ຕ້ອງການການຄວບຄຸມທີ່ຊັດເຈນຫຼາຍຂອງເສັ້ນທາງຕັດ, ໂດຍສະເພາະໃນເຂດວົງຈອນທີ່ມີຄວາມຫນາແຫນ້ນສູງ, ບ່ອນທີ່ deviations ເລັກນ້ອຍສາມາດເຮັດໃຫ້ chip ຫຼາຍຜິດປົກກະຕິ. ນອກຈາກນັ້ນ, wafers ຂະຫນາດໃຫຍ່ປະກອບດ້ວຍເສັ້ນຕັດຫຼາຍແລະຂັ້ນຕອນຂະບວນການທີ່ສັບສົນຫຼາຍ, ຈໍາເປັນຕ້ອງໄດ້ປັບປຸງເພີ່ມເຕີມໃນຄວາມແມ່ນຍໍາ, ຄວາມສອດຄ່ອງ, ແລະປະສິດທິພາບຂອງເຕັກໂນໂລຊີ dicing ເພື່ອຕອບສະຫນອງສິ່ງທ້າທາຍເຫຼົ່ານີ້.
1.3 ຂະບວນການ Dicing Wafer
ຂະບວນການເຮັດເຄັກ wafer ກວມເອົາທຸກຂັ້ນຕອນຈາກຂັ້ນຕອນການກະກຽມຈົນເຖິງການກວດກາຄຸນນະພາບຂັ້ນສຸດທ້າຍ, ໂດຍແຕ່ລະຂັ້ນຕອນແມ່ນສໍາຄັນຕໍ່ການຮັບປະກັນຄຸນນະພາບແລະການປະຕິບັດຂອງຊິບ diced. ຂ້າງລຸ່ມນີ້ແມ່ນຄໍາອະທິບາຍລາຍລະອຽດຂອງແຕ່ລະໄລຍະ.
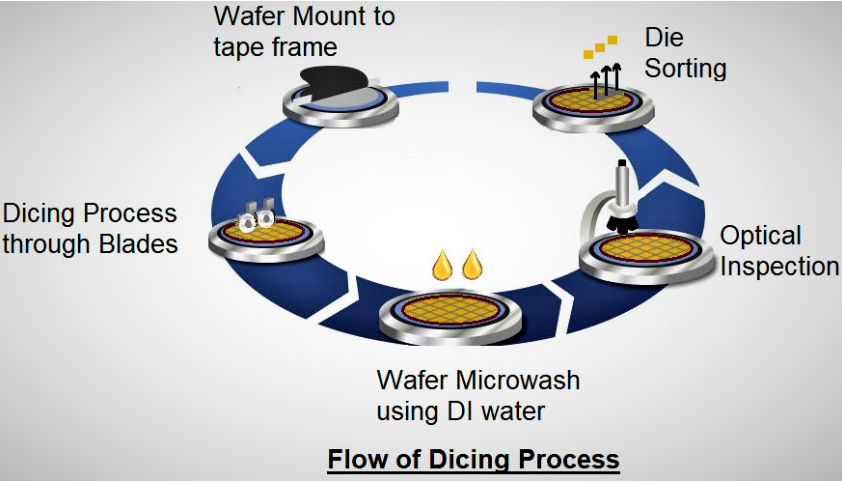
ໄລຍະ | ລາຍລະອຽດ |
ໄລຍະການກະກຽມ | -Wafer ທໍາຄວາມສະອາດ: ໃຊ້ນ້ໍາທີ່ມີຄວາມບໍລິສຸດສູງແລະສານທໍາຄວາມສະອາດພິເສດ, ສົມທົບກັບການຂັດດ້ວຍ ultrasonic ຫຼືກົນຈັກ, ເພື່ອເອົາ impurities, particles, ແລະສິ່ງປົນເປື້ອນ, ຮັບປະກັນດ້ານສະອາດ. -ການຈັດຕໍາແຫນ່ງທີ່ຊັດເຈນ: ໃຊ້ອຸປະກອນທີ່ມີຄວາມແມ່ນຍໍາສູງເພື່ອຮັບປະກັນວ່າ wafer ຖືກແບ່ງຢ່າງຖືກຕ້ອງຕາມເສັ້ນທາງຕັດທີ່ອອກແບບ. -ການສ້ອມແຊມ Wafer: ຍຶດ wafer ໃສ່ກອບ tape ເພື່ອຮັກສາຄວາມຫມັ້ນຄົງໃນລະຫວ່າງການຕັດ, ປ້ອງກັນຄວາມເສຍຫາຍຈາກການສັ່ນສະເທືອນຫຼືການເຄື່ອນໄຫວ. |
ໄລຍະການຕັດ | -ໃບມີດຕັດ: ໃຊ້ແຜ່ນໃບຄ້າຍຄືເພັດຫມຸນທີ່ມີຄວາມໄວສູງສໍາລັບການຕັດທາງດ້ານຮ່າງກາຍ, ເຫມາະສົມກັບວັດສະດຸທີ່ໃຊ້ຊິລິໂຄນແລະປະຫຍັດຄ່າໃຊ້ຈ່າຍ. -Laser Dicing: ໃຊ້ເລເຊີທີ່ມີພະລັງງານສູງສໍາລັບການຕັດບໍ່ຕິດຕໍ່, ເຫມາະສໍາລັບວັດສະດຸ brittle ຫຼື hardness ສູງເຊັ່ນ: gallium nitride, ສະເຫນີຄວາມແມ່ນຍໍາສູງແລະການສູນເສຍວັດສະດຸຫນ້ອຍ. -ເຕັກໂນໂລຊີໃໝ່: ແນະນຳເທັກໂນໂລຍີການຕັດດ້ວຍເລເຊີ ແລະ plasma ເພື່ອປັບປຸງປະສິດທິພາບ ແລະຄວາມແມ່ນຍໍາ ໃນຂະນະທີ່ຫຼຸດພື້ນທີ່ທີ່ໄດ້ຮັບຜົນກະທົບຈາກຄວາມຮ້ອນ. |
ໄລຍະທຳຄວາມສະອາດ | - ໃຊ້ນ້ໍາ deionized (ນ້ໍາ DI) ແລະຕົວແທນທໍາຄວາມສະອາດພິເສດ, ສົມທົບກັບການທໍາຄວາມສະອາດ ultrasonic ຫຼືສີດພົ່ນ, ເພື່ອເອົາ debris ແລະຂີ້ຝຸ່ນທີ່ສ້າງຂຶ້ນໃນລະຫວ່າງການຕັດ, ປ້ອງກັນການຕົກຄ້າງຈາກຜົນກະທົບຕໍ່ຂະບວນການຕໍ່ໄປຫຼື chip ປະສິດທິພາບໄຟຟ້າ. - ນ້ໍາ DI ຄວາມບໍລິສຸດສູງຫຼີກເວັ້ນການນໍາສະເຫນີສິ່ງປົນເປື້ອນໃຫມ່, ຮັບປະກັນສະພາບແວດລ້ອມ wafer ສະອາດ. |
ໄລຍະການກວດກາ | -ການກວດກາ Optical: ໃຊ້ລະບົບກວດຈັບ optical ສົມທົບກັບ AI algorithms ເພື່ອກໍານົດຂໍ້ບົກພ່ອງຢ່າງວ່ອງໄວ, ຮັບປະກັນບໍ່ມີຮອຍແຕກຫຼື chipping ໃນ chip diced, ປັບປຸງປະສິດທິພາບການກວດສອບ, ແລະຫຼຸດຜ່ອນຄວາມຜິດພາດຂອງມະນຸດ. -ການວັດແທກຂະຫນາດ: ກວດສອບວ່າຂະໜາດຊິບກົງກັບການອອກແບບສະເພາະ. -ການທົດສອບປະສິດທິພາບໄຟຟ້າ: ຮັບປະກັນປະສິດທິພາບໄຟຟ້າຂອງຊິບທີ່ສໍາຄັນໄດ້ມາດຕະຖານ, ຮັບປະກັນຄວາມຫນ້າເຊື່ອຖືໃນຄໍາຮ້ອງສະຫມັກຕໍ່ໄປ. |
ໄລຍະການຈັດລຽງ | - ໃຊ້ແຂນຫຸ່ນຍົນຫຼືຈອກດູດສູນຍາກາດເພື່ອແຍກຊິບທີ່ມີຄຸນນະພາບອອກຈາກກອບເທບແລະຈັດຮຽງອັດຕະໂນມັດໂດຍອີງໃສ່ການປະຕິບັດ, ຮັບປະກັນປະສິດທິພາບການຜະລິດແລະຄວາມຍືດຫຍຸ່ນໃນຂະນະທີ່ປັບປຸງຄວາມແມ່ນຍໍາ. |
ຂະບວນການຕັດ wafer ປະກອບດ້ວຍການເຮັດຄວາມສະອາດ wafer, ການຈັດຕໍາແຫນ່ງ, ການຕັດ, ການເຮັດຄວາມສະອາດ, ການກວດກາ, ແລະການຈັດລຽງ, ໂດຍແຕ່ລະຂັ້ນຕອນແມ່ນສໍາຄັນ. ດ້ວຍຄວາມກ້າວຫນ້າໃນລະບົບອັດຕະໂນມັດ, ການຕັດ laser, ແລະເຕັກໂນໂລຊີການກວດສອບ AI, ລະບົບການຕັດ wafer ທີ່ທັນສະໄຫມສາມາດບັນລຸຄວາມແມ່ນຍໍາສູງ, ຄວາມໄວ, ແລະການສູນເສຍວັດສະດຸຕ່ໍາ. ໃນອະນາຄົດ, ເຕັກໂນໂລຊີການຕັດໃຫມ່ເຊັ່ນ laser ແລະ plasma ຈະຄ່ອຍໆທົດແທນການຕັດແຜ່ນໃບຄ້າຍຄືແບບດັ້ງເດີມເພື່ອຕອບສະຫນອງຄວາມຕ້ອງການຂອງການອອກແບບ chip ສະລັບສັບຊ້ອນທີ່ເພີ່ມຂຶ້ນ, ຊຸກຍູ້ການພັດທະນາຂອງຂະບວນການຜະລິດ semiconductor.
ເຕັກໂນໂລຊີການຕັດ Wafer ແລະຫຼັກການຂອງມັນ
ຮູບພາບສະແດງໃຫ້ເຫັນສາມເຕັກໂນໂລຊີການຕັດ wafer ທົ່ວໄປ:ໃບມີດຕັດ,Laser Dicing, ແລະPlasma Dicing. ຂ້າງລຸ່ມນີ້ແມ່ນການວິເຄາະລາຍລະອຽດແລະຄໍາອະທິບາຍເພີ່ມເຕີມຂອງສາມເຕັກນິກເຫຼົ່ານີ້:
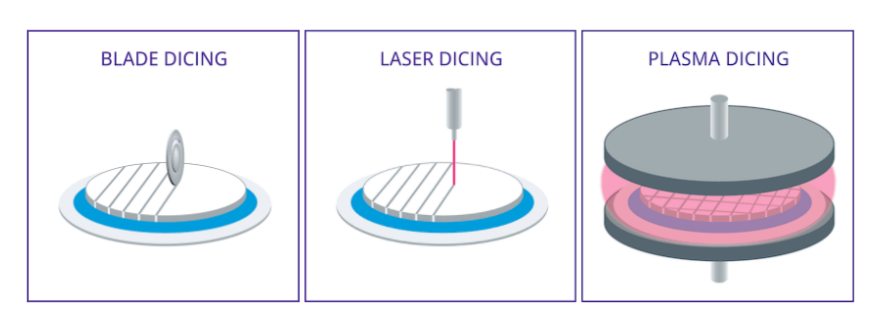
ໃນການຜະລິດ semiconductor, ການຕັດ wafer ແມ່ນຂັ້ນຕອນສໍາຄັນທີ່ຮຽກຮ້ອງໃຫ້ມີການເລືອກວິທີການຕັດທີ່ເຫມາະສົມໂດຍອີງໃສ່ຄວາມຫນາຂອງ wafer. ຂັ້ນຕອນທໍາອິດແມ່ນການກໍານົດຄວາມຫນາຂອງ wafer. ຖ້າຄວາມຫນາຂອງ wafer ເກີນ 100 microns, ແຜ່ນໃບຄ້າຍຄືສາມາດເລືອກເປັນວິທີການຕັດ. ຖ້າການຕັດດ້ວຍແຜ່ນໃບບໍ່ເຫມາະສົມ, ສາມາດນໍາໃຊ້ວິທີການຕັດກະດູກຫັກ, ເຊິ່ງປະກອບມີທັງເຕັກນິກການຕັດ scribe ແລະຕັດແຜ່ນໃບ.
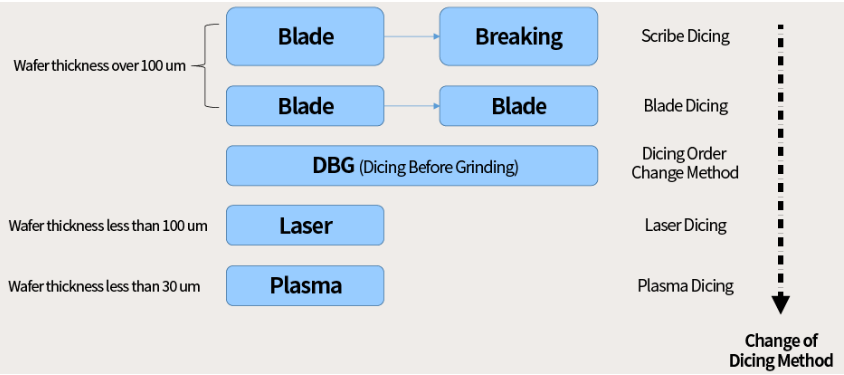
ເມື່ອຄວາມຫນາຂອງ wafer ຢູ່ໃນລະຫວ່າງ 30 ຫາ 100 microns, ແນະນໍາວິທີການ DBG (Dice ກ່ອນ Grinding). ໃນກໍລະນີນີ້, ການຕັດ scribe, ໃບມີດຕັດ, ຫຼືປັບລໍາດັບການຕັດຕາມຄວາມຕ້ອງການສາມາດໄດ້ຮັບການຄັດເລືອກເພື່ອບັນລຸຜົນໄດ້ຮັບທີ່ດີທີ່ສຸດ.
ສໍາລັບ wafers ບາງໆທີ່ມີຄວາມຫນາຫນ້ອຍກວ່າ 30 microns, ການຕັດ laser ກາຍເປັນວິທີການທີ່ຕ້ອງການເນື່ອງຈາກຄວາມສາມາດໃນການຕັດ wafers ບາງໆໄດ້ຊັດເຈນໂດຍບໍ່ມີການເຮັດໃຫ້ເກີດຄວາມເສຍຫາຍຫຼາຍເກີນໄປ. ຖ້າການຕັດ laser ບໍ່ສາມາດຕອບສະຫນອງຄວາມຕ້ອງການສະເພາະ, ການຕັດ plasma ສາມາດນໍາໃຊ້ເປັນທາງເລືອກ. ຕາຕະລາງການໄຫຼວຽນນີ້ສະຫນອງເສັ້ນທາງການຕັດສິນໃຈທີ່ຊັດເຈນເພື່ອຮັບປະກັນເຕັກນິກການຕັດ wafer ທີ່ເຫມາະສົມທີ່ສຸດຖືກເລືອກພາຍໃຕ້ເງື່ອນໄຂຄວາມຫນາທີ່ແຕກຕ່າງກັນ.
2.1 ເຕັກໂນໂລຊີການຕັດດ້ວຍກົນຈັກ
ເຕັກໂນໂລຍີການຕັດດ້ວຍກົນຈັກແມ່ນວິທີການພື້ນເມືອງໃນ wafer dicing. ຫຼັກການຫຼັກແມ່ນໃຊ້ລໍ້ຫມຸນເພັດທີ່ມີຄວາມໄວສູງເປັນເຄື່ອງມືຕັດເພື່ອຕັດ wafer. ອຸປະກອນຫຼັກປະກອບມີ spindle ທີ່ມີອາກາດ, ເຊິ່ງເຮັດໃຫ້ເຄື່ອງມືລໍ້ຂັດເພັດດ້ວຍຄວາມໄວສູງເພື່ອປະຕິບັດການຕັດຫຼືຮ່ອງທີ່ຊັດເຈນຕາມເສັ້ນທາງຕັດທີ່ກໍານົດໄວ້ກ່ອນ. ເຕັກໂນໂລຊີນີ້ຖືກນໍາໃຊ້ຢ່າງກວ້າງຂວາງໃນອຸດສາຫະກໍາເນື່ອງຈາກຄ່າໃຊ້ຈ່າຍຕ່ໍາ, ປະສິດທິພາບສູງ, ແລະການນໍາໃຊ້ຢ່າງກວ້າງຂວາງ.
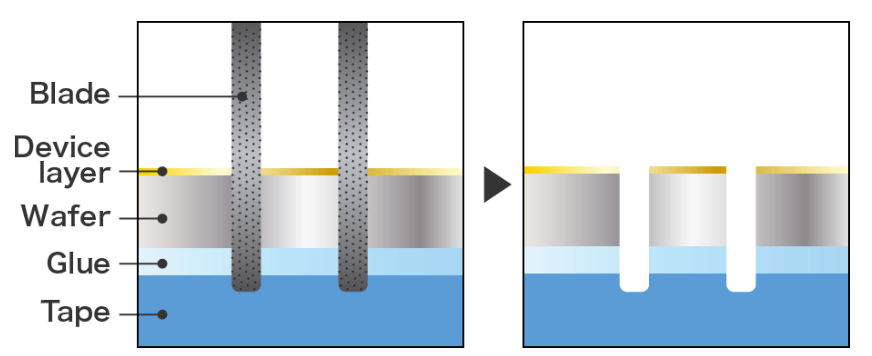
ຂໍ້ດີ
ຄວາມແຂງສູງແລະຄວາມທົນທານຕໍ່ການສວມໃສ່ຂອງເຄື່ອງມືລໍ້ຂັດເພັດເຮັດໃຫ້ເຕັກໂນໂລຢີການຕັດກົນຈັກສາມາດປັບຕົວເຂົ້າກັບຄວາມຕ້ອງການຕັດຂອງວັດສະດຸ wafer ຕ່າງໆ, ບໍ່ວ່າຈະເປັນວັດສະດຸທີ່ໃຊ້ຊິລິໂຄນແບບດັ້ງເດີມຫຼື semiconductors ປະສົມໃຫມ່. ການດໍາເນີນງານຂອງມັນແມ່ນງ່າຍດາຍ, ມີຄວາມຕ້ອງການດ້ານວິຊາການຂ້ອນຂ້າງຕ່ໍາ, ສົ່ງເສີມຄວາມນິຍົມຂອງຕົນໃນການຜະລິດຈໍານວນຫລາຍ. ນອກຈາກນັ້ນ, ເມື່ອປຽບທຽບກັບວິທີການຕັດອື່ນໆເຊັ່ນການຕັດດ້ວຍເລເຊີ, ການຕັດກົນຈັກມີຄ່າໃຊ້ຈ່າຍທີ່ສາມາດຄວບຄຸມໄດ້ຫຼາຍ, ເຮັດໃຫ້ມັນເຫມາະສົມກັບຄວາມຕ້ອງການການຜະລິດທີ່ມີປະລິມານສູງ.
ຂໍ້ຈໍາກັດ
ເຖິງວ່າຈະມີຂໍ້ໄດ້ປຽບຈໍານວນຫລາຍ, ເຕັກໂນໂລຊີການຕັດກົນຈັກຍັງມີຂໍ້ຈໍາກັດ. ຫນ້າທໍາອິດ, ເນື່ອງຈາກການຕິດຕໍ່ທາງດ້ານຮ່າງກາຍລະຫວ່າງເຄື່ອງມືແລະ wafer, ຄວາມແມ່ນຍໍາຂອງການຕັດແມ່ນຂ້ອນຂ້າງຈໍາກັດ, ມັກຈະນໍາໄປສູ່ການບິດເບືອນມິຕິລະດັບທີ່ສາມາດສົ່ງຜົນກະທົບຕໍ່ຄວາມຖືກຕ້ອງຂອງການຫຸ້ມຫໍ່ chip ຕໍ່ມາແລະການທົດສອບ. ອັນທີສອງ, ຂໍ້ບົກພ່ອງເຊັ່ນ: chipping ແລະ cracks ສາມາດເກີດຂຶ້ນໄດ້ຢ່າງງ່າຍດາຍໃນລະຫວ່າງການຂະບວນການຕັດກົນຈັກ, ເຊິ່ງບໍ່ພຽງແຕ່ຜົນກະທົບຕໍ່ອັດຕາຜົນຜະລິດ, ແຕ່ຍັງມີຜົນກະທົບທາງລົບຕໍ່ຄວາມຫນ້າເຊື່ອຖືແລະອາຍຸການຂອງ chip ໄດ້. ຄວາມເສຍຫາຍທີ່ເກີດຈາກຄວາມກົດດັນທາງກົນແມ່ນເປັນອັນຕະລາຍໂດຍສະເພາະການຜະລິດຊິບທີ່ມີຄວາມຫນາແຫນ້ນສູງ, ໂດຍສະເພາະໃນເວລາທີ່ການຕັດວັດສະດຸທີ່ແຕກຫັກ, ເຊິ່ງບັນຫາເຫຼົ່ານີ້ແມ່ນໂດດເດັ່ນກວ່າ.
ການປັບປຸງເຕັກໂນໂລຢີ
ເພື່ອເອົາຊະນະຂໍ້ຈໍາກັດເຫຼົ່ານີ້, ນັກຄົ້ນຄວ້າກໍາລັງປັບປຸງຂະບວນການຕັດກົນຈັກຢ່າງຕໍ່ເນື່ອງ. ການປັບປຸງທີ່ສໍາຄັນລວມມີການເພີ່ມການອອກແບບແລະການຄັດເລືອກວັດສະດຸຂອງລໍ້ grinding ເພື່ອປັບປຸງຄວາມແມ່ນຍໍາຂອງການຕັດແລະຄວາມທົນທານ. ນອກຈາກນັ້ນ, ການເພີ່ມປະສິດທິພາບຂອງການອອກແບບໂຄງສ້າງແລະລະບົບການຄວບຄຸມຂອງອຸປະກອນຕັດໄດ້ປັບປຸງຄວາມຫມັ້ນຄົງແລະອັດຕະໂນມັດຂອງຂະບວນການຕັດ. ຄວາມກ້າວຫນ້າເຫຼົ່ານີ້ຫຼຸດຜ່ອນຄວາມຜິດພາດທີ່ເກີດຈາກການດໍາເນີນງານຂອງມະນຸດແລະປັບປຸງຄວາມສອດຄ່ອງຂອງການຕັດ. ການນໍາສະເຫນີເຕັກໂນໂລຢີການກວດກາແລະການຄວບຄຸມຄຸນນະພາບທີ່ກ້າວຫນ້າສໍາລັບການກວດສອບຄວາມຜິດປົກກະຕິໃນເວລາທີ່ແທ້ຈິງໃນລະຫວ່າງການຂະບວນການຕັດຍັງໄດ້ປັບປຸງຄວາມຫນ້າເຊື່ອຖືຂອງການຕັດແລະຜົນຜະລິດຢ່າງຫຼວງຫຼາຍ.
ການພັດທະນາໃນອະນາຄົດແລະເຕັກໂນໂລຢີໃຫມ່
ເຖິງແມ່ນວ່າເຕັກໂນໂລຊີການຕັດກົນຈັກຍັງຖືຕໍາແຫນ່ງທີ່ສໍາຄັນໃນການຕັດ wafer, ເຕັກໂນໂລຊີການຕັດໃຫມ່ແມ່ນກ້າວຫນ້າຢ່າງໄວວາໃນຂະນະທີ່ຂະບວນການ semiconductor ພັດທະນາ. ສໍາລັບຕົວຢ່າງ, ຄໍາຮ້ອງສະຫມັກຂອງເຕັກໂນໂລຊີການຕັດ laser ຄວາມຮ້ອນສະຫນອງການແກ້ໄຂໃຫມ່ເພື່ອຄວາມແມ່ນຍໍາແລະຂໍ້ບົກພ່ອງໃນການຕັດກົນຈັກ. ວິທີການຕັດທີ່ບໍ່ຕິດຕໍ່ນີ້ຊ່ວຍຫຼຸດຜ່ອນຄວາມກົດດັນທາງດ້ານຮ່າງກາຍໃນ wafer, ຫຼຸດລົງຢ່າງຫຼວງຫຼາຍຂອງການເກີດຮອຍແຕກແລະການແຕກ, ໂດຍສະເພາະໃນເວລາທີ່ການຕັດວັດສະດຸ brittle ຫຼາຍ. ໃນອະນາຄົດ, ການປະສົມປະສານຂອງເຕັກໂນໂລຊີການຕັດກົນຈັກກັບເຕັກນິກການຕັດທີ່ພົ້ນເດັ່ນຂື້ນຈະຊ່ວຍໃຫ້ການຜະລິດ semiconductor ມີທາງເລືອກແລະຄວາມຍືດຫຍຸ່ນຫຼາຍຂຶ້ນ, ເພີ່ມປະສິດທິພາບການຜະລິດແລະຄຸນນະພາບຂອງຊິບ.
ສະຫຼຸບແລ້ວ, ເຖິງແມ່ນວ່າເຕັກໂນໂລຊີການຕັດກົນຈັກມີຂໍ້ບົກຜ່ອງທີ່ແນ່ນອນ, ການປັບປຸງເຕັກໂນໂລຢີຢ່າງຕໍ່ເນື່ອງແລະການເຊື່ອມໂຍງກັບເຕັກນິກການຕັດໃຫມ່ຊ່ວຍໃຫ້ມັນຍັງຄົງມີບົດບາດສໍາຄັນໃນການຜະລິດ semiconductor ແລະຮັກສາຄວາມສາມາດໃນການແຂ່ງຂັນໃນຂະບວນການໃນອະນາຄົດ.
2.2 ເຕັກໂນໂລຊີການຕັດດ້ວຍເລເຊີ
ເທກໂນໂລຍີການຕັດເລເຊີ, ເປັນວິທີການໃຫມ່ໃນການຕັດ wafer, ຄ່ອຍໆໄດ້ຮັບຄວາມສົນໃຈຢ່າງກວ້າງຂວາງໃນອຸດສາຫະກໍາ semiconductor ເນື່ອງຈາກຄວາມແມ່ນຍໍາສູງ, ຂາດຄວາມເສຍຫາຍຕິດຕໍ່ກົນຈັກ, ແລະຄວາມສາມາດໃນການຕັດຢ່າງໄວວາ. ເທກໂນໂລຍີນີ້ໃຊ້ຄວາມຫນາແຫນ້ນຂອງພະລັງງານສູງແລະຄວາມສາມາດໃນການສຸມໃສ່ຂອງລໍາແສງເລເຊີເພື່ອສ້າງເຂດທີ່ຖືກກະທົບຄວາມຮ້ອນຂະຫນາດນ້ອຍຢູ່ເທິງພື້ນຜິວຂອງວັດສະດຸ wafer. ໃນເວລາທີ່ beam laser ຖືກນໍາໃຊ້ກັບ wafer ໄດ້, ຄວາມກົດດັນຄວາມຮ້ອນທີ່ສ້າງຂຶ້ນເຮັດໃຫ້ອຸປະກອນການກະດູກຫັກຢູ່ສະຖານທີ່ກໍານົດ, ບັນລຸການຕັດທີ່ຊັດເຈນ.
ຂໍ້ໄດ້ປຽບຂອງເຕັກໂນໂລຊີການຕັດ Laser
• ຄວາມຊັດເຈນສູງ: ຄວາມສາມາດໃນການຕັ້ງຕໍາແຫນ່ງທີ່ຊັດເຈນຂອງ laser beam ອະນຸຍາດໃຫ້ຕັດ micron ຫຼືແມ້ກະທັ້ງລະດັບ nanometer, ຕອບສະຫນອງຄວາມຕ້ອງການຂອງການຜະລິດວົງຈອນປະສົມປະສານທີ່ມີຄວາມແມ່ນຍໍາສູງທີ່ທັນສະໄຫມ.
•ບໍ່ມີການຕິດຕໍ່ກົນຈັກ: ການຕັດດ້ວຍເລເຊີຫຼີກລ້ຽງການຕິດຕໍ່ທາງດ້ານຮ່າງກາຍກັບ wafer, ປ້ອງກັນບັນຫາທົ່ວໄປໃນການຕັດກົນຈັກ, ເຊັ່ນ: chipping ແລະ cracking, ຢ່າງຫຼວງຫຼາຍປັບປຸງອັດຕາຜົນຜະລິດແລະຄວາມຫນ້າເຊື່ອຖືຂອງ chip ໄດ້.
•ຄວາມໄວຕັດໄວ: ຄວາມໄວສູງຂອງການຕັດ laser ປະກອບສ່ວນເຂົ້າໃນການເພີ່ມປະສິດທິພາບການຜະລິດ, ເຮັດໃຫ້ມັນເຫມາະສົມໂດຍສະເພາະສໍາລັບສະຖານະການການຜະລິດຂະຫນາດໃຫຍ່, ຄວາມໄວສູງ.
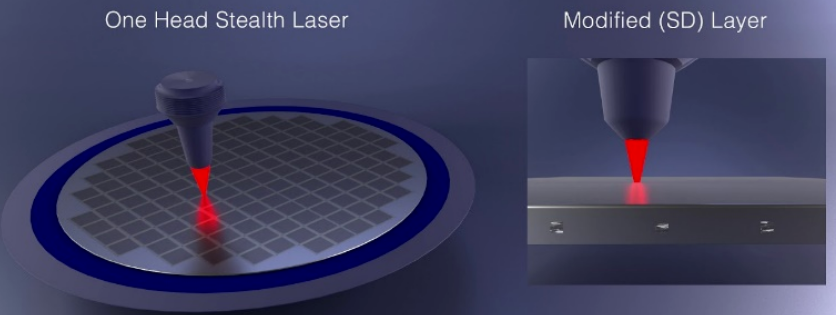
ສິ່ງທ້າທາຍທີ່ປະເຊີນ
•ຄ່າໃຊ້ຈ່າຍອຸປະກອນສູງ: ການລົງທຶນເບື້ອງຕົ້ນສໍາລັບອຸປະກອນຕັດ laser ແມ່ນສູງ, ເຊິ່ງສະເຫນີຄວາມກົດດັນດ້ານເສດຖະກິດ, ໂດຍສະເພາະສໍາລັບວິສາຫະກິດການຜະລິດຂະຫນາດນ້ອຍແລະຂະຫນາດກາງ.
•ການຄວບຄຸມຂະບວນການສະລັບສັບຊ້ອນ: ການຕັດດ້ວຍເລເຊີຮຽກຮ້ອງໃຫ້ມີການຄວບຄຸມທີ່ຊັດເຈນຂອງພາລາມິເຕີຫຼາຍອັນ, ລວມທັງຄວາມຫນາແຫນ້ນຂອງພະລັງງານ, ຕໍາແຫນ່ງຈຸດສຸມ, ແລະຄວາມໄວຂອງການຕັດ, ເຮັດໃຫ້ຂະບວນການສັບສົນ.
• ບັນຫາເຂດທີ່ໄດ້ຮັບຜົນກະທົບຈາກຄວາມຮ້ອນ: ເຖິງແມ່ນວ່າລັກສະນະທີ່ບໍ່ແມ່ນການຕິດຕໍ່ຂອງການຕັດ laser ຈະຫຼຸດຜ່ອນຄວາມເສຍຫາຍທາງກົນ, ຄວາມກົດດັນຄວາມຮ້ອນທີ່ເກີດຈາກເຂດທີ່ໄດ້ຮັບຜົນກະທົບຈາກຄວາມຮ້ອນ (HAZ) ສາມາດສົ່ງຜົນກະທົບທາງລົບຕໍ່ຄຸນສົມບັດຂອງວັດສະດຸ wafer. ການເພີ່ມປະສິດທິພາບເພີ່ມເຕີມຂອງຂະບວນການແມ່ນຈໍາເປັນເພື່ອຫຼຸດຜ່ອນຜົນກະທົບນີ້.
ທິດທາງການປັບປຸງເຕັກໂນໂລຢີ
ເພື່ອແກ້ໄຂສິ່ງທ້າທາຍເຫຼົ່ານີ້, ນັກຄົ້ນຄວ້າໄດ້ສຸມໃສ່ການຫຼຸດຜ່ອນຄ່າໃຊ້ຈ່າຍອຸປະກອນ, ປັບປຸງປະສິດທິພາບການຕັດ, ແລະເພີ່ມປະສິດທິພາບການໄຫຼຂອງຂະບວນການ.
•ເລເຊີທີ່ມີປະສິດທິພາບແລະລະບົບ Optical: ໂດຍການພັດທະນາ lasers ປະສິດທິພາບຫຼາຍແລະລະບົບ optical ກ້າວຫນ້າ, ມັນເປັນໄປໄດ້ທີ່ຈະຫຼຸດລົງຄ່າໃຊ້ຈ່າຍອຸປະກອນໃນຂະນະທີ່ເພີ່ມຄວາມແມ່ນຍໍາຂອງການຕັດແລະຄວາມໄວ.
•ການເພີ່ມປະສິດທິພາບພາລາມິເຕີຂະບວນການ: ການຄົ້ນຄວ້າໃນຄວາມເລິກກ່ຽວກັບການພົວພັນລະຫວ່າງເລເຊີແລະວັດສະດຸ wafer ໄດ້ຖືກດໍາເນີນເພື່ອປັບປຸງຂະບວນການທີ່ຫຼຸດຜ່ອນເຂດທີ່ໄດ້ຮັບຜົນກະທົບຈາກຄວາມຮ້ອນ, ດັ່ງນັ້ນການປັບປຸງຄຸນນະພາບການຕັດ.
• ລະບົບຄວບຄຸມອັດສະລິຍະ: ການພັດທະນາເທກໂນໂລຍີການຄວບຄຸມອັດສະລິຍະມີຈຸດປະສົງເພື່ອອັດຕະໂນມັດແລະເພີ່ມປະສິດທິພາບຂະບວນການຕັດເລເຊີ, ປັບປຸງຄວາມຫມັ້ນຄົງແລະຄວາມສອດຄ່ອງຂອງມັນ.
ເທກໂນໂລຍີການຕັດດ້ວຍເລເຊີແມ່ນມີປະສິດທິພາບໂດຍສະເພາະໃນ wafers ບາງໆແລະສະຖານະການຕັດທີ່ມີຄວາມແມ່ນຍໍາສູງ. ໃນຂະນະທີ່ຂະຫນາດຂອງ wafer ເພີ່ມຂຶ້ນແລະຄວາມຫນາແຫນ້ນຂອງວົງຈອນເພີ່ມຂຶ້ນ, ວິທີການຕັດກົນຈັກແບບດັ້ງເດີມມີຄວາມຫຍຸ້ງຍາກເພື່ອຕອບສະຫນອງຄວາມຕ້ອງການທີ່ມີຄວາມແມ່ນຍໍາສູງແລະປະສິດທິພາບສູງຂອງການຜະລິດ semiconductor ທີ່ທັນສະໄຫມ. ເນື່ອງຈາກຂໍ້ໄດ້ປຽບທີ່ເປັນເອກະລັກຂອງຕົນ, ການຕັດ laser ໄດ້ກາຍເປັນການແກ້ໄຂທີ່ຕ້ອງການໃນຂົງເຂດເຫຼົ່ານີ້.
ເຖິງແມ່ນວ່າເທກໂນໂລຍີການຕັດ laser ຍັງປະເຊີນກັບສິ່ງທ້າທາຍເຊັ່ນຄ່າໃຊ້ຈ່າຍອຸປະກອນສູງແລະຄວາມຊັບຊ້ອນຂອງຂະບວນການ, ຄວາມໄດ້ປຽບທີ່ເປັນເອກະລັກຂອງຕົນໃນຄວາມແມ່ນຍໍາສູງແລະຄວາມເສຍຫາຍທີ່ບໍ່ແມ່ນການຕິດຕໍ່ເຮັດໃຫ້ມັນເປັນທິດທາງທີ່ສໍາຄັນສໍາລັບການພັດທະນາໃນການຜະລິດ semiconductor. ໃນຂະນະທີ່ເຕັກໂນໂລຊີ laser ແລະລະບົບການຄວບຄຸມອັດສະລິຍະສືບຕໍ່ກ້າວຫນ້າ, ການຕັດ laser ຄາດວ່າຈະປັບປຸງປະສິດທິພາບການຕັດ wafer ແລະຄຸນນະພາບ, ຂັບລົດການພັດທະນາຢ່າງຕໍ່ເນື່ອງຂອງອຸດສາຫະກໍາ semiconductor.
2.3 ເຕັກໂນໂລຊີການຕັດ Plasma
ເຕັກໂນໂລຊີການຕັດ plasma, ເປັນວິທີການ wafer dicing ທີ່ພົ້ນເດັ່ນຂື້ນ, ໄດ້ຮັບຄວາມສົນໃຈຢ່າງຫຼວງຫຼາຍໃນຊຸມປີມໍ່ໆມານີ້. ເທກໂນໂລຍີນີ້ໃຊ້ beam plasma ພະລັງງານສູງເພື່ອຕັດ wafers ຢ່າງແນ່ນອນໂດຍການຄວບຄຸມພະລັງງານ, ຄວາມໄວ, ແລະເສັ້ນທາງຕັດຂອງ beam plasma, ບັນລຸຜົນການຕັດທີ່ດີທີ່ສຸດ.
ຫຼັກການການເຮັດວຽກແລະຂໍ້ໄດ້ປຽບ
ຂະບວນການຕັດ plasma ແມ່ນອີງໃສ່ beam plasma ທີ່ມີອຸນຫະພູມສູງ, ພະລັງງານສູງທີ່ຜະລິດໂດຍອຸປະກອນ. beam ນີ້ສາມາດໃຫ້ຄວາມຮ້ອນຂອງວັດສະດຸ wafer ກັບຈຸດ melting ຫຼື vaporization ຂອງຕົນໃນຈໍານວນສັ້ນຂອງທີ່ໃຊ້ເວລາ, ເຮັດໃຫ້ການຕັດໄວ. ເມື່ອປຽບທຽບກັບການຕັດກົນຈັກຫຼືເລເຊີແບບດັ້ງເດີມ, ການຕັດ plasma ແມ່ນໄວກວ່າແລະຜະລິດເຂດທີ່ໄດ້ຮັບຜົນກະທົບຈາກຄວາມຮ້ອນຂະຫນາດນ້ອຍກວ່າ, ປະສິດທິຜົນຫຼຸດຜ່ອນການເກີດຮອຍແຕກແລະຄວາມເສຍຫາຍໃນລະຫວ່າງການຕັດ.
ໃນການປະຕິບັດຕົວຈິງ, ເຕັກໂນໂລຢີການຕັດ plasma ແມ່ນມີຄວາມຊໍານານໂດຍສະເພາະໃນການຈັດການ wafers ທີ່ມີຮູບຮ່າງທີ່ສັບສົນ. ມັນມີພະລັງງານສູງ, beam plasma ທີ່ສາມາດປັບໄດ້ໄດ້ຢ່າງງ່າຍດາຍສາມາດຕັດ wafers ຮູບຮ່າງສະຫມໍ່າສະເຫມີທີ່ມີຄວາມແມ່ນຍໍາສູງ. ດັ່ງນັ້ນ, ໃນການຜະລິດຈຸນລະພາກ, ໂດຍສະເພາະໃນການຜະລິດແບບປັບແຕ່ງແລະຂະຫນາດນ້ອຍຂອງຊິບລະດັບສູງ, ເຕັກໂນໂລຢີນີ້ສະແດງໃຫ້ເຫັນຄໍາສັນຍາທີ່ຍິ່ງໃຫຍ່ສໍາລັບການນໍາໃຊ້ຢ່າງກວ້າງຂວາງ.
ສິ່ງທ້າທາຍແລະຂໍ້ຈໍາກັດ
ເຖິງວ່າຈະມີຄວາມໄດ້ປຽບຫຼາຍຂອງເຕັກໂນໂລຊີການຕັດ plasma, ມັນຍັງປະເຊີນກັບສິ່ງທ້າທາຍບາງຢ່າງ.
•ຂະບວນການສະລັບສັບຊ້ອນ: ຂະບວນການຕັດ plasma ແມ່ນສະລັບສັບຊ້ອນແລະຕ້ອງການອຸປະກອນທີ່ມີຄວາມແມ່ນຍໍາສູງແລະຜູ້ປະຕິບັດງານທີ່ມີປະສົບການເພື່ອຮັບປະກັນຄວາມຖືກຕ້ອງແລະຄວາມຫມັ້ນຄົງໃນການຕັດ.
• ການຄວບຄຸມ ແລະ ຄວາມປອດໄພດ້ານສິ່ງແວດລ້ອມ: ອຸນຫະພູມສູງ, ລັກສະນະພະລັງງານສູງຂອງ beam plasma ຮຽກຮ້ອງໃຫ້ມີການຄວບຄຸມສິ່ງແວດລ້ອມທີ່ເຂັ້ມງວດແລະມາດຕະການຄວາມປອດໄພ, ເຊິ່ງເພີ່ມຄວາມສັບສົນແລະຄ່າໃຊ້ຈ່າຍໃນການປະຕິບັດ.
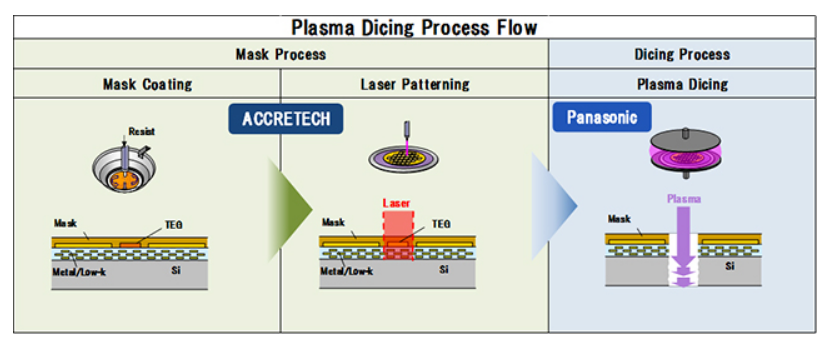
ທິດທາງການພັດທະນາໃນອະນາຄົດ
ດ້ວຍຄວາມກ້າວຫນ້າທາງດ້ານເຕັກໂນໂລຢີ, ສິ່ງທ້າທາຍທີ່ກ່ຽວຂ້ອງກັບການຕັດ plasma ຄາດວ່າຈະໄດ້ຮັບການແກ້ໄຂເທື່ອລະກ້າວ. ໂດຍການພັດທະນາອຸປະກອນການຕັດທີ່ສະຫລາດແລະມີຄວາມຫມັ້ນຄົງຫຼາຍ, ການເພິ່ງພາອາໄສການດໍາເນີນການຄູ່ມືສາມາດຫຼຸດລົງ, ດັ່ງນັ້ນການປັບປຸງປະສິດທິພາບການຜະລິດ. ໃນເວລາດຽວກັນ, ການເພີ່ມປະສິດທິພາບຂອງຕົວກໍານົດການຂະບວນການແລະສະພາບແວດລ້ອມການຕັດຈະຊ່ວຍໃຫ້ຄວາມສ່ຽງດ້ານຄວາມປອດໄພຕ່ໍາແລະຄ່າໃຊ້ຈ່າຍໃນການດໍາເນີນງານ.
ໃນອຸດສາຫະກໍາ semiconductor, ການປະດິດສ້າງໃນການຕັດ wafer ແລະເຕັກໂນໂລຊີ dicing ແມ່ນສໍາຄັນຕໍ່ການຂັບລົດການພັດທະນາຂອງອຸດສາຫະກໍາ. ເທກໂນໂລຍີການຕັດ plasma, ມີຄວາມແມ່ນຍໍາສູງ, ປະສິດທິພາບ, ແລະຄວາມສາມາດໃນການຈັດການຮູບຮ່າງຂອງ wafer ສະລັບສັບຊ້ອນ, ໄດ້ກາຍມາເປັນຜູ້ນໃຫມ່ທີ່ສໍາຄັນໃນພາກສະຫນາມນີ້. ເຖິງວ່າຍັງມີບາງສິ່ງທ້າທາຍຢູ່, ແຕ່ບັນດາບັນຫານີ້ຈະໄດ້ຮັບການແກ້ໄຂເທື່ອລະກ້າວດ້ວຍການສືບຕໍ່ປະດິດສ້າງເຕັກໂນໂລຢີ, ນຳມາເຊິ່ງຄວາມເປັນໄປໄດ້ ແລະ ກາລະໂອກາດໃຫ້ແກ່ການຜະລິດສານເຄິ່ງຕົວນຳ.
ຄວາມສົດໃສດ້ານຂອງຄໍາຮ້ອງສະຫມັກຂອງເຕັກໂນໂລຊີການຕັດ plasma ແມ່ນກວ້າງຂວາງ, ແລະຄາດວ່າຈະມີບົດບາດສໍາຄັນຫຼາຍໃນການຜະລິດ semiconductor ໃນອະນາຄົດ. ໂດຍຜ່ານການປະດິດສ້າງເຕັກໂນໂລຢີຢ່າງຕໍ່ເນື່ອງແລະການເພີ່ມປະສິດທິພາບ, ການຕັດ plasma ບໍ່ພຽງແຕ່ຈະແກ້ໄຂສິ່ງທ້າທາຍທີ່ມີຢູ່ເທົ່ານັ້ນ, ແຕ່ຍັງກາຍເປັນຕົວຂັບເຄື່ອນທີ່ມີປະສິດທິພາບໃນການເຕີບໂຕຂອງອຸດສາຫະກໍາ semiconductor.
2.4 ການຕັດຄຸນນະພາບແລະປັດໃຈທີ່ມີອິດທິພົນ
ຄຸນນະພາບການຕັດ wafer ແມ່ນສໍາຄັນສໍາລັບການຫຸ້ມຫໍ່ chip ຕໍ່ໄປ, ການທົດສອບ, ແລະປະສິດທິພາບໂດຍລວມແລະຄວາມຫນ້າເຊື່ອຖືຂອງຜະລິດຕະພັນສຸດທ້າຍ. ບັນຫາທົ່ວໄປທີ່ພົບໃນລະຫວ່າງການຕັດປະກອບມີຮອຍແຕກ, ການຕັດ, ແລະຄວາມແຕກຕ່າງຂອງການຕັດ. ບັນຫາເຫຼົ່ານີ້ແມ່ນມີອິດທິພົນຈາກປັດໃຈຈໍານວນຫນຶ່ງທີ່ເຮັດວຽກຮ່ວມກັນ.
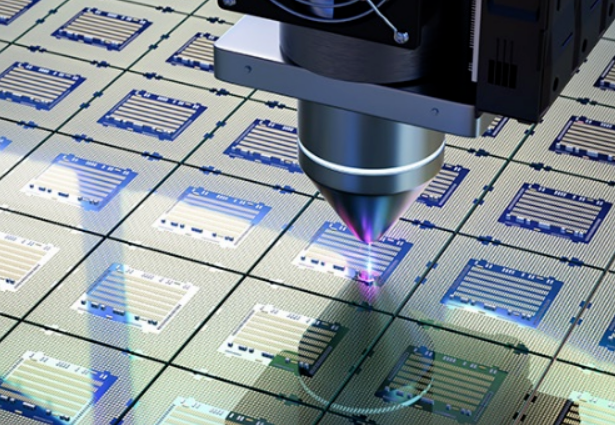
ປະເພດ | ເນື້ອໃນ | ຜົນກະທົບ |
ຕົວກໍານົດການຂະບວນການ | ຄວາມໄວຕັດ, ອັດຕາການໃຫ້ອາຫານ, ແລະຄວາມເລິກຂອງການຕັດໂດຍກົງຜົນກະທົບຕໍ່ຄວາມຫມັ້ນຄົງແລະຄວາມແມ່ນຍໍາຂອງຂະບວນການຕັດ. ການຕັ້ງຄ່າທີ່ບໍ່ຖືກຕ້ອງສາມາດນໍາໄປສູ່ຄວາມເຂັ້ມຂົ້ນຂອງຄວາມກົດດັນແລະເຂດທີ່ໄດ້ຮັບຜົນກະທົບຈາກຄວາມຮ້ອນຫຼາຍເກີນໄປ, ເຮັດໃຫ້ເກີດຮອຍແຕກແລະແຕກ. ການປັບຕົວກໍານົດການທີ່ເຫມາະສົມໂດຍອີງໃສ່ວັດສະດຸ wafer, ຄວາມຫນາ, ແລະຄວາມຕ້ອງການການຕັດແມ່ນສໍາຄັນເພື່ອບັນລຸຜົນການຕັດທີ່ຕ້ອງການ. | ຕົວກໍານົດການຂະບວນການທີ່ຖືກຕ້ອງຮັບປະກັນການຕັດທີ່ຊັດເຈນແລະຫຼຸດຜ່ອນຄວາມສ່ຽງຂອງຂໍ້ບົກພ່ອງເຊັ່ນ: ຮອຍແຕກແລະການ chipping. |
ປັດໃຈອຸປະກອນ ແລະວັດສະດຸ | -ຄຸນະພາບຂອງແຜ່ນໃບຄ້າຍຄື: ວັດສະດຸ, ຄວາມແຂງ, ແລະຄວາມຕ້ານທານຂອງແຜ່ນໃບມີອິດທິພົນຕໍ່ຄວາມລຽບຂອງຂະບວນການຕັດແລະຄວາມຮາບພຽງຢູ່ດ້ານຕັດ. ແຜ່ນໃບມີຄຸນນະພາບບໍ່ດີເພີ່ມຄວາມເຄັ່ງຕຶງ ແລະ ຄວາມດັນຄວາມຮ້ອນ, ອາດຈະເຮັດໃຫ້ເກີດຮອຍແຕກ ຫຼື ແຕກ. ການເລືອກວັດສະດຸແຜ່ນໃບທີ່ເຫມາະສົມແມ່ນສໍາຄັນ. -ປະສິດທິພາບເຄື່ອງເຮັດຄວາມເຢັນ: ເຄື່ອງເຮັດຄວາມເຢັນຊ່ວຍຫຼຸດອຸນຫະພູມການຕັດ, ຫຼຸດຜ່ອນການສຽດສີ, ແລະລ້າງສິ່ງເສດເຫຼືອ. ນໍ້າເຢັນທີ່ບໍ່ມີປະສິດຕິຜົນສາມາດນໍາໄປສູ່ອຸນຫະພູມສູງແລະການສ້າງຂີ້ເຫຍື້ອ, ຜົນກະທົບຕໍ່ຄຸນນະພາບແລະປະສິດທິພາບການຕັດ. ການເລືອກເຄື່ອງເຮັດຄວາມເຢັນທີ່ມີປະສິດທິພາບ ແລະເປັນມິດກັບສິ່ງແວດລ້ອມແມ່ນສໍາຄັນ. | ຄຸນະພາບຂອງແຜ່ນໃບມີຜົນຕໍ່ຄວາມແມ່ນຍໍາແລະຄວາມລຽບຂອງການຕັດ. ນໍ້າເຢັນທີ່ບໍ່ມີປະສິດຕິຜົນສາມາດສົ່ງຜົນໃຫ້ມີຄຸນນະພາບການຕັດແລະປະສິດທິພາບທີ່ບໍ່ດີ, ຊີ້ໃຫ້ເຫັນເຖິງຄວາມຕ້ອງການສໍາລັບການນໍາໃຊ້ coolant ທີ່ດີທີ່ສຸດ. |
ການຄວບຄຸມຂະບວນການແລະການກວດກາຄຸນນະພາບ | -ການຄວບຄຸມຂະບວນການ: ການຕິດຕາມເວລາທີ່ແທ້ຈິງແລະການປັບຕົວກໍານົດການຕັດທີ່ສໍາຄັນເພື່ອຮັບປະກັນຄວາມຫມັ້ນຄົງແລະຄວາມສອດຄ່ອງໃນຂະບວນການຕັດ. -ການກວດກາຄຸນນະພາບ: ການກວດສອບຮູບລັກສະນະຫລັງການຕັດ, ການວັດແທກຂະຫນາດ, ແລະການທົດສອບການປະຕິບັດທາງໄຟຟ້າຊ່ວຍກໍານົດແລະແກ້ໄຂບັນຫາທີ່ມີຄຸນນະພາບທັນທີ, ປັບປຸງຄວາມຖືກຕ້ອງຂອງການຕັດແລະຄວາມສອດຄ່ອງ. | ການຄວບຄຸມຂະບວນການທີ່ຖືກຕ້ອງແລະການກວດສອບຄຸນນະພາບຊ່ວຍໃຫ້ຜົນໄດ້ຮັບການຕັດທີ່ສອດຄ່ອງ, ມີຄຸນນະພາບສູງແລະການຄົ້ນພົບບັນຫາທີ່ອາດຈະເກີດຂື້ນໃນຕົ້ນປີ. |

ການປັບປຸງຄຸນນະພາບການຕັດ
ການປັບປຸງຄຸນນະພາບການຕັດຮຽກຮ້ອງໃຫ້ມີວິທີການທີ່ສົມບູນແບບທີ່ຄໍານຶງເຖິງຕົວກໍານົດການຂະບວນການ, ອຸປະກອນແລະການຄັດເລືອກວັດສະດຸ, ການຄວບຄຸມຂະບວນການ, ແລະການກວດກາ. ໂດຍການປັບປຸງເຕັກໂນໂລຢີການຕັດຢ່າງຕໍ່ເນື່ອງແລະວິທີການຂະບວນການເພີ່ມປະສິດທິພາບ, ຄວາມແມ່ນຍໍາແລະຄວາມຫມັ້ນຄົງຂອງການຕັດ wafer ສາມາດປັບປຸງຕື່ມອີກ, ສະຫນອງການສະຫນັບສະຫນູນດ້ານວິຊາການທີ່ເຊື່ອຖືໄດ້ຫຼາຍສໍາລັບອຸດສາຫະກໍາການຜະລິດ semiconductor.
#03 ການຈັດການຫຼັງການຕັດ ແລະ ການທົດສອບ
3.1 ການທໍາຄວາມສະອາດແລະການອົບແຫ້ງ
ຂັ້ນຕອນການທໍາຄວາມສະອາດແລະການຕາກແຫ້ງຫຼັງຈາກການຕັດ wafer ແມ່ນສໍາຄັນສໍາລັບການຮັບປະກັນຄຸນນະພາບຂອງຊິບແລະຄວາມກ້າວຫນ້າຂອງຂະບວນການຕໍ່ໄປ. ໃນລະຫວ່າງຂັ້ນຕອນນີ້, ມັນເປັນສິ່ງຈໍາເປັນທີ່ຈະຕ້ອງເອົາສິ່ງເສດເຫຼືອຂອງຊິລິໂຄນ, ຕົກຄ້າງຂອງ coolant, ແລະສິ່ງປົນເປື້ອນອື່ນໆທີ່ສ້າງຂຶ້ນໃນລະຫວ່າງການຕັດ. ມັນເປັນສິ່ງສໍາຄັນເທົ່າທຽມກັນເພື່ອຮັບປະກັນວ່າຊິບບໍ່ເສຍຫາຍໃນລະຫວ່າງການທໍາຄວາມສະອາດ, ແລະຫຼັງຈາກເວລາແຫ້ງ, ໃຫ້ແນ່ໃຈວ່າບໍ່ມີຄວາມຊຸ່ມຊື່ນຢູ່ໃນຫນ້າຂອງຊິບເພື່ອປ້ອງກັນບັນຫາຕ່າງໆເຊັ່ນການກັດກ່ອນຫຼືການໄຫຼຂອງ electrostatic.
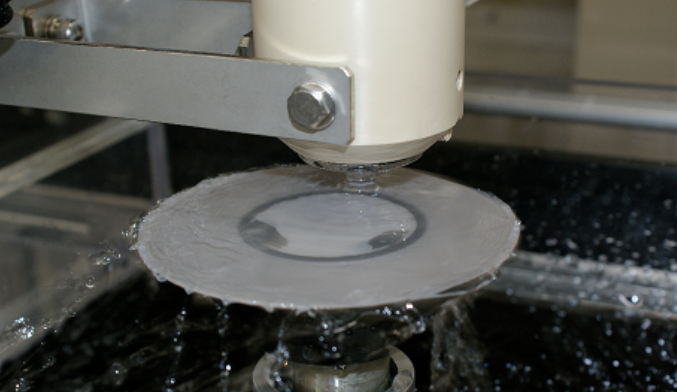
ການຈັດການຫຼັງການຕັດ: ຂະບວນການທໍາຄວາມສະອາດແລະການອົບແຫ້ງ
ຂັ້ນຕອນຂະບວນການ | ເນື້ອໃນ | ຜົນກະທົບ |
ຂະບວນການທໍາຄວາມສະອາດ | -ວິທີການ: ໃຊ້ຕົວແທນທໍາຄວາມສະອາດພິເສດແລະນ້ໍາບໍລິສຸດ, ສົມທົບກັບເຕັກນິກການແປງ ultrasonic ຫຼືກົນຈັກສໍາລັບການທໍາຄວາມສະອາດ. | ຮັບປະກັນການກໍາຈັດສິ່ງປົນເປື້ອນຢ່າງລະອຽດແລະປ້ອງກັນຄວາມເສຍຫາຍຂອງຊິບໃນລະຫວ່າງການເຮັດຄວາມສະອາດ. |
-ການຄັດເລືອກຕົວແທນທໍາຄວາມສະອາດ: ເລືອກໂດຍອີງໃສ່ວັດສະດຸ wafer ແລະປະເພດການປົນເປື້ອນເພື່ອຮັບປະກັນການທໍາຄວາມສະອາດທີ່ມີປະສິດທິພາບໂດຍບໍ່ມີການທໍາລາຍຊິບ. | ການຄັດເລືອກຕົວແທນທີ່ເຫມາະສົມແມ່ນສໍາຄັນສໍາລັບການທໍາຄວາມສະອາດປະສິດທິພາບແລະການປ້ອງກັນ chip. | |
-ການຄວບຄຸມພາລາມິເຕີ: ຄວບຄຸມອຸນຫະພູມການເຮັດຄວາມສະອາດຢ່າງເຂັ້ມງວດ, ເວລາ, ແລະຄວາມເຂັ້ມຂຸ້ນຂອງການແກ້ໄຂການເຮັດຄວາມສະອາດເພື່ອປ້ອງກັນບັນຫາທີ່ມີຄຸນນະພາບທີ່ເກີດຈາກການເຮັດຄວາມສະອາດທີ່ບໍ່ຖືກຕ້ອງ. | ການຄວບຄຸມຊ່ວຍຫຼີກເວັ້ນການທໍາລາຍ wafer ຫຼືເຮັດໃຫ້ສິ່ງປົນເປື້ອນຢູ່ຫລັງ, ຮັບປະກັນຄຸນນະພາບທີ່ສອດຄ່ອງ. | |
ຂະບວນການອົບແຫ້ງ | -ວິທີການແບບດັ້ງເດີມ: ການອົບແຫ້ງອາກາດທໍາມະຊາດແລະການອົບແຫ້ງດ້ວຍອາກາດຮ້ອນ, ເຊິ່ງມີປະສິດທິພາບຕ່ໍາແລະສາມາດນໍາໄປສູ່ການສ້າງໄຟຟ້າສະຖິດ. | ອາດຈະເຮັດໃຫ້ເວລາແຫ້ງຊ້າລົງ ແລະບັນຫາຄົງທີ່ທີ່ອາດຈະເກີດຂຶ້ນ. |
-ເຕັກໂນໂລຊີທີ່ທັນສະໄຫມ: ໃຊ້ເທກໂນໂລຍີຂັ້ນສູງເຊັ່ນ: ການອົບແຫ້ງສູນຍາກາດແລະການອົບແຫ້ງດ້ວຍອິນຟາເລດເພື່ອຮັບປະກັນວ່າຊິບແຫ້ງໄວແລະຫຼີກເວັ້ນຜົນກະທົບທີ່ເປັນອັນຕະລາຍ. | ຂະບວນການອົບແຫ້ງໄວຂຶ້ນ ແລະມີປະສິດທິພາບຫຼາຍຂຶ້ນ, ຫຼຸດຜ່ອນຄວາມສ່ຽງຕໍ່ການໄຫຼວຽນຂອງສະຖິດ ຫຼືບັນຫາທີ່ກ່ຽວຂ້ອງກັບຄວາມຊຸ່ມ. | |
ການຄັດເລືອກອຸປະກອນແລະການບໍາລຸງຮັກສາ | -ການຄັດເລືອກອຸປະກອນ: ເຄື່ອງເຮັດຄວາມສະອາດແລະການອົບແຫ້ງທີ່ມີປະສິດທິພາບສູງປັບປຸງປະສິດທິພາບການປຸງແຕ່ງແລະລະອຽດຄວບຄຸມບັນຫາທີ່ອາດເກີດຂື້ນໃນລະຫວ່າງການຈັດການ. | ເຄື່ອງຈັກທີ່ມີຄຸນນະພາບສູງຮັບປະກັນການປຸງແຕ່ງທີ່ດີກວ່າແລະຫຼຸດຜ່ອນຄວາມເປັນໄປໄດ້ຂອງຄວາມຜິດພາດໃນລະຫວ່າງການເຮັດຄວາມສະອາດແລະການອົບແຫ້ງ. |
-ການບໍາລຸງຮັກສາອຸປະກອນ: ການກວດກາປົກກະຕິແລະການບໍາລຸງຮັກສາອຸປະກອນໃຫ້ແນ່ໃຈວ່າມັນຍັງຄົງຢູ່ໃນສະພາບການເຮັດວຽກທີ່ດີທີ່ສຸດ, ຮັບປະກັນຄຸນນະພາບຂອງຊິບ. | ການບໍາລຸງຮັກສາທີ່ເຫມາະສົມປ້ອງກັນຄວາມລົ້ມເຫຼວຂອງອຸປະກອນ, ຮັບປະກັນການປຸງແຕ່ງທີ່ເຊື່ອຖືໄດ້ແລະມີຄຸນນະພາບສູງ. |
ການທໍາຄວາມສະອາດຫລັງການຕັດແລະການອົບແຫ້ງ
ຂັ້ນຕອນການທໍາຄວາມສະອາດແລະການອົບແຫ້ງຫຼັງຈາກການຕັດ wafer ແມ່ນຂະບວນການທີ່ສັບສົນແລະລະອຽດອ່ອນທີ່ຮຽກຮ້ອງໃຫ້ມີການພິຈາລະນາຢ່າງລະອຽດຂອງປັດໃຈຫຼາຍເພື່ອຮັບປະກັນຜົນໄດ້ຮັບຂອງການປຸງແຕ່ງສຸດທ້າຍ. ໂດຍການນໍາໃຊ້ວິທີການວິທະຍາສາດແລະຂັ້ນຕອນທີ່ເຄັ່ງຄັດ, ມັນເປັນໄປໄດ້ທີ່ຈະຮັບປະກັນວ່າແຕ່ລະຊິບເຂົ້າໄປໃນຂັ້ນຕອນການຫຸ້ມຫໍ່ແລະການທົດສອບຕໍ່ໄປໃນສະພາບທີ່ດີທີ່ສຸດ.
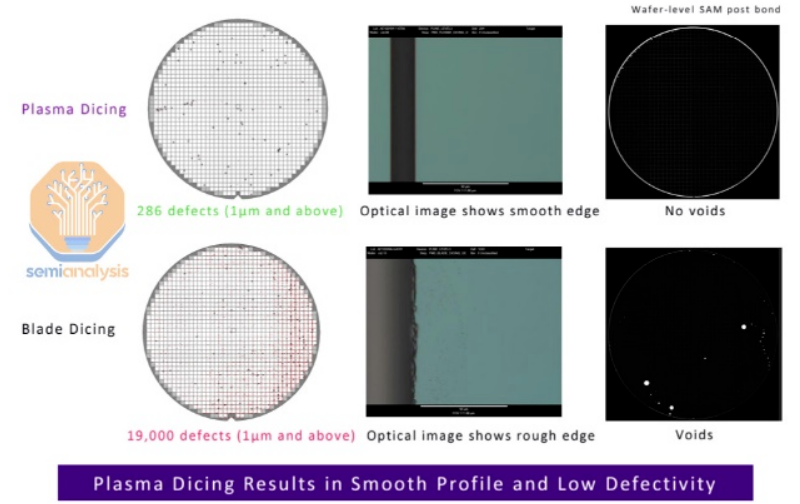
ການກວດສອບແລະການທົດສອບຫຼັງການຕັດ
ຂັ້ນຕອນ | ເນື້ອໃນ | ຜົນກະທົບ |
ຂັ້ນຕອນການກວດກາ | 1.ການກວດກາສາຍຕາ: ໃຊ້ອຸປະກອນກວດກາດ້ວຍສາຍຕາ ຫຼື ອັດຕະໂນມັດເພື່ອກວດສອບຂໍ້ບົກພ່ອງທີ່ເຫັນໄດ້ ເຊັ່ນ: ຮອຍແຕກ, ແຕກ, ຫຼືການປົນເປື້ອນຢູ່ດ້ານຂອງຊິບ. ກໍານົດ chip ທີ່ເສຍຫາຍທາງຮ່າງກາຍຢ່າງໄວວາເພື່ອຫຼີກເວັ້ນການເສຍ. | ຊ່ວຍໃນການກໍານົດແລະກໍາຈັດ chip ຜິດປົກກະຕິໃນຕອນຕົ້ນຂອງຂະບວນການ, ຫຼຸດຜ່ອນການສູນເສຍວັດສະດຸ. |
2.ການວັດແທກຂະຫນາດ: ໃຊ້ອຸປະກອນວັດແທກຄວາມແມ່ນຍໍາເພື່ອວັດແທກຂະຫນາດຊິບຢ່າງຖືກຕ້ອງ, ຮັບປະກັນຂະຫນາດຕັດກົງກັບການອອກແບບສະເພາະແລະປ້ອງກັນບັນຫາການປະຕິບັດຫຼືຄວາມຫຍຸ້ງຍາກໃນການຫຸ້ມຫໍ່. | ໃຫ້ແນ່ໃຈວ່າຊິບຢູ່ໃນຂອບເຂດຈໍາກັດຂະຫນາດທີ່ຕ້ອງການ, ປ້ອງກັນການເຊື່ອມໂຊມຂອງການປະຕິບັດຫຼືບັນຫາການປະກອບ. | |
3.ການທົດສອບປະສິດທິພາບໄຟຟ້າ: ປະເມີນຕົວກໍານົດການໄຟຟ້າທີ່ສໍາຄັນເຊັ່ນ: ຄວາມຕ້ານທານ, capacitance, ແລະ inductance, ເພື່ອກໍານົດ chip ທີ່ບໍ່ສອດຄ່ອງແລະຮັບປະກັນພຽງແຕ່ chip ປະສິດທິພາບດໍາເນີນການກັບຂັ້ນຕອນຕໍ່ໄປ. | ຮັບປະກັນວ່າຊິບທີ່ເຮັດວຽກ ແລະ ທົດສອບປະສິດທິພາບພຽງແຕ່ກ້າວໄປຂ້າງໜ້າໃນຂະບວນການ, ຫຼຸດຜ່ອນຄວາມສ່ຽງຂອງຄວາມລົ້ມເຫຼວໃນຂັ້ນຕອນຕໍ່ມາ. | |
ຂັ້ນຕອນການທົດສອບ | 1.ການທົດສອບການທໍາງານ: ກວດສອບວ່າການທໍາງານພື້ນຖານຂອງ chip ໄດ້ເຮັດວຽກຕາມຈຸດປະສົງ, ການກໍານົດແລະການກໍາຈັດ chip ທີ່ມີຄວາມຜິດປົກກະຕິການທໍາງານ. | ຮັບປະກັນວ່າຊິບຕອບສະໜອງໄດ້ຄວາມຕ້ອງການຂັ້ນພື້ນຖານໃນການດໍາເນີນງານກ່ອນທີ່ຈະກ້າວໄປສູ່ຂັ້ນຕອນຕໍ່ມາ. |
2.ການທົດສອບຄວາມຫນ້າເຊື່ອຖື: ປະເມີນຄວາມສະຖຽນຂອງປະສິດທິພາບຂອງຊິບພາຍໃຕ້ການໃຊ້ເປັນເວລາດົນນານ ຫຼືສະພາບແວດລ້ອມທີ່ຮຸນແຮງ, ໂດຍທົ່ວໄປແລ້ວຈະກ່ຽວຂ້ອງກັບຄວາມແກ່ຂອງອຸນຫະພູມສູງ, ການທົດສອບອຸນຫະພູມຕໍ່າ ແລະການທົດສອບຄວາມຊຸ່ມຊື່ນເພື່ອຈຳລອງສະພາບທີ່ຮຸນແຮງໃນໂລກຕົວຈິງ. | ຮັບປະກັນວ່າຊິບສາມາດເຮັດວຽກໄດ້ຢ່າງໜ້າເຊື່ອຖືພາຍໃຕ້ເງື່ອນໄຂສິ່ງແວດລ້ອມຫຼາຍປະເພດ, ປັບປຸງຄວາມທົນທານຂອງຜະລິດຕະພັນ ແລະ ຄວາມໝັ້ນຄົງ. | |
3.ການທົດສອບຄວາມເຂົ້າກັນໄດ້: ກວດສອບວ່າຊິບເຮັດວຽກໄດ້ຢ່າງຖືກຕ້ອງກັບອົງປະກອບຫຼືລະບົບອື່ນໆ, ຮັບປະກັນວ່າບໍ່ມີຄວາມຜິດພາດຫຼືການຫຼຸດຜ່ອນການປະຕິບັດເນື່ອງຈາກຄວາມບໍ່ເຂົ້າກັນໄດ້. | ຮັບປະກັນການໃຊ້ງານທີ່ລຽບງ່າຍໃນແອັບພລິເຄຊັນຕົວຈິງ ໂດຍການປ້ອງກັນບັນຫາຄວາມເຂົ້າກັນໄດ້. |
3.3 ການຫຸ້ມຫໍ່ແລະການເກັບຮັກສາ
ຫຼັງຈາກການຕັດ wafer, chip ແມ່ນຜົນຜະລິດທີ່ສໍາຄັນຂອງຂະບວນການຜະລິດ semiconductor, ແລະຂັ້ນຕອນການຫຸ້ມຫໍ່ແລະການເກັບຮັກສາຂອງເຂົາເຈົ້າມີຄວາມສໍາຄັນເທົ່າທຽມກັນ. ການຫຸ້ມຫໍ່ແລະການເກັບຮັກສາທີ່ເຫມາະສົມແມ່ນມີຄວາມຈໍາເປັນບໍ່ພຽງແຕ່ສໍາລັບການຮັບປະກັນຄວາມປອດໄພແລະຄວາມຫມັ້ນຄົງຂອງຊິບໃນລະຫວ່າງການຂົນສົ່ງແລະການເກັບຮັກສາ, ແຕ່ຍັງສໍາລັບການສະຫນອງການສະຫນັບສະຫນູນທີ່ເຂັ້ມແຂງສໍາລັບການຜະລິດ, ການທົດສອບແລະການຫຸ້ມຫໍ່ຕໍ່ມາ.
ສະຫຼຸບຂັ້ນຕອນການກວດກາ ແລະ ທົດສອບ:
ຂັ້ນຕອນການກວດສອບແລະການທົດສອບສໍາລັບຊິບຫຼັງຈາກການຕັດ wafer ກວມເອົາຫຼາຍດ້ານ, ລວມທັງການກວດກາສາຍຕາ, ການວັດແທກຂະຫນາດ, ການທົດສອບປະສິດທິພາບໄຟຟ້າ, ການທົດສອບການເຮັດວຽກ, ການທົດສອບຄວາມຫນ້າເຊື່ອຖື, ແລະການທົດສອບຄວາມເຂົ້າກັນໄດ້. ຂັ້ນຕອນເຫຼົ່ານີ້ແມ່ນມີການເຊື່ອມຕໍ່ກັນແລະເສີມສ້າງເປັນສິ່ງກີດຂວາງທີ່ເຂັ້ມແຂງເພື່ອຮັບປະກັນຄຸນນະພາບຜະລິດຕະພັນແລະຄວາມຫມັ້ນຄົງ. ໂດຍຜ່ານຂັ້ນຕອນການກວດກາແລະການທົດສອບຢ່າງເຂັ້ມງວດ, ບັນຫາທີ່ອາດສາມາດຖືກກໍານົດແລະແກ້ໄຂໄດ້ທັນທີ, ຮັບປະກັນຜະລິດຕະພັນສຸດທ້າຍຕອບສະຫນອງຄວາມຕ້ອງການຂອງລູກຄ້າແລະຄວາມຄາດຫວັງ.
ລັກສະນະ | ເນື້ອໃນ |
ມາດຕະການການຫຸ້ມຫໍ່ | 1.ຕ້ານສະຖິດ: ອຸປະກອນການຫຸ້ມຫໍ່ຄວນມີຄຸນສົມບັດຕ້ານການສະຖິດທີ່ດີເລີດເພື່ອປ້ອງກັນບໍ່ໃຫ້ໄຟຟ້າສະຖິດຈາກການທໍາລາຍອຸປະກອນຫຼືຜົນກະທົບຕໍ່ການປະຕິບັດຂອງມັນ. |
2.ປ້ອງກັນຄວາມຊຸ່ມຊື່ນ: ວັດສະດຸຫຸ້ມຫໍ່ຄວນມີຄວາມທົນທານຕໍ່ຄວາມຊຸ່ມຊື່ນທີ່ດີເພື່ອປ້ອງກັນການກັດກ່ອນແລະການເສື່ອມສະພາບຂອງການປະຕິບັດໄຟຟ້າທີ່ເກີດຈາກຄວາມຊຸ່ມຊື່ນ. | |
3.ກັນສັ່ນ: ວັດສະດຸຫຸ້ມຫໍ່ຄວນສະຫນອງການດູດຊຶມຊ໊ອກທີ່ມີປະສິດທິພາບເພື່ອປົກປ້ອງຊິບຈາກການສັ່ນສະເທືອນແລະຜົນກະທົບໃນລະຫວ່າງການຂົນສົ່ງ. | |
ສະພາບແວດລ້ອມການເກັບຮັກສາ | 1.ການຄວບຄຸມຄວາມຊຸ່ມຊື່ນ: ຄວບຄຸມຄວາມຊຸ່ມຊື່ນຢ່າງເຂັ້ມງວດພາຍໃນຂອບເຂດທີ່ເຫມາະສົມເພື່ອປ້ອງກັນການດູດຊຶມຄວາມຊຸ່ມຊື່ນແລະການກັດກ່ອນທີ່ເກີດຈາກຄວາມຊຸ່ມຊື່ນຫຼາຍເກີນໄປຫຼືບັນຫາຄົງທີ່ທີ່ເກີດຈາກຄວາມຊຸ່ມຊື່ນຕ່ໍາ. |
2.ຄວາມສະອາດ: ຮັກສາສະພາບແວດລ້ອມການເກັບຮັກສາທີ່ສະອາດເພື່ອຫຼີກເວັ້ນການປົນເປື້ອນຂອງ chip ໂດຍຂີ້ຝຸ່ນແລະ impurities. | |
3.ການຄວບຄຸມອຸນຫະພູມ: ກໍານົດລະດັບອຸນຫະພູມທີ່ສົມເຫດສົມຜົນແລະຮັກສາຄວາມຫມັ້ນຄົງຂອງອຸນຫະພູມເພື່ອປ້ອງກັນການເລັ່ງການອາຍຸເນື່ອງຈາກຄວາມຮ້ອນເກີນໄປຫຼືບັນຫາການ condensation ທີ່ເກີດຈາກອຸນຫະພູມຕ່ໍາ. | |
ການກວດກາປົກກະຕິ | ເປັນປົກກະຕິກວດກາແລະປະເມີນຊິບເກັບຮັກສາໄວ້, ການນໍາໃຊ້ການກວດກາສາຍຕາ, ການວັດແທກຂະຫນາດ, ແລະການທົດສອບປະສິດທິພາບໄຟຟ້າເພື່ອກໍານົດແລະແກ້ໄຂບັນຫາທີ່ອາດຈະເກີດຂຶ້ນໄດ້ທັນເວລາ. ອີງຕາມເວລາແລະເງື່ອນໄຂການເກັບຮັກສາ, ວາງແຜນການນໍາໃຊ້ຊິບເພື່ອຮັບປະກັນວ່າພວກມັນຖືກນໍາໃຊ້ໃນສະພາບທີ່ດີທີ່ສຸດ. |
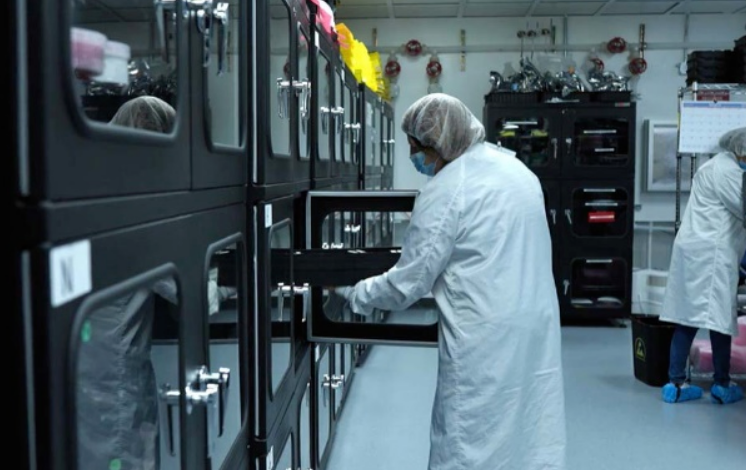
ບັນຫາຂອງ microcracks ແລະຄວາມເສຍຫາຍໃນລະຫວ່າງການຂະບວນການ wafer dicing ແມ່ນສິ່ງທ້າທາຍທີ່ສໍາຄັນໃນການຜະລິດ semiconductor. ຄວາມກົດດັນຂອງການຕັດແມ່ນສາເຫດຕົ້ນຕໍຂອງປະກົດການນີ້, ຍ້ອນວ່າມັນສ້າງຮອຍແຕກຂະຫນາດນ້ອຍແລະຄວາມເສຍຫາຍຂອງຫນ້າດິນ wafer, ເຮັດໃຫ້ຄ່າໃຊ້ຈ່າຍໃນການຜະລິດເພີ່ມຂຶ້ນແລະການຫຼຸດລົງຂອງຄຸນນະພາບຂອງຜະລິດຕະພັນ.
ເພື່ອແກ້ໄຂສິ່ງທ້າທາຍນີ້, ມັນເປັນສິ່ງ ສຳ ຄັນທີ່ຈະຫຼຸດຜ່ອນຄວາມກົດດັນໃນການຕັດແລະປະຕິບັດເຕັກນິກການຕັດ, ເຄື່ອງມືແລະເງື່ອນໄຂທີ່ດີທີ່ສຸດ. ການເອົາໃຈໃສ່ຢ່າງລະມັດລະວັງຕໍ່ປັດໃຈເຊັ່ນ: ວັດສະດຸແຜ່ນໃບ, ຄວາມໄວຕັດ, ຄວາມກົດດັນ, ແລະວິທີການເຮັດຄວາມເຢັນສາມາດຊ່ວຍຫຼຸດຜ່ອນການສ້າງ microcracks ແລະປັບປຸງຜົນຜະລິດໂດຍລວມຂອງຂະບວນການ. ນອກຈາກນັ້ນ, ການຄົ້ນຄວ້າຢ່າງຕໍ່ເນື່ອງກ່ຽວກັບເຕັກໂນໂລຢີການຕັດທີ່ກ້າວຫນ້າ, ເຊັ່ນ: laser dicing, ກໍາລັງຄົ້ນຫາວິທີການເພື່ອຫຼຸດຜ່ອນບັນຫາເຫຼົ່ານີ້ຕື່ມອີກ.
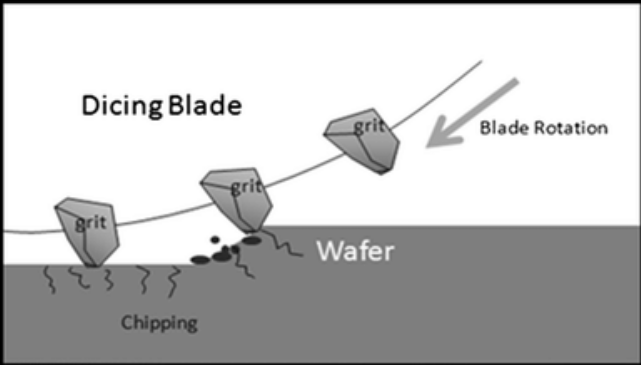
ໃນຖານະເປັນວັດສະດຸທີ່ອ່ອນແອ, wafers ມີຄວາມສ່ຽງຕໍ່ການປ່ຽນແປງໂຄງສ້າງພາຍໃນເມື່ອຖືກຄວາມກົດດັນທາງກົນຈັກ, ຄວາມຮ້ອນ, ຫຼືທາງເຄມີ, ນໍາໄປສູ່ການສ້າງຕັ້ງຂອງ microcracks. ເຖິງແມ່ນວ່າຮອຍແຕກເຫຼົ່ານີ້ອາດຈະບໍ່ສັງເກດເຫັນໄດ້ທັນທີ, ແຕ່ພວກມັນສາມາດຂະຫຍາຍອອກແລະເຮັດໃຫ້ເກີດຄວາມເສຍຫາຍທີ່ຮ້າຍແຮງກວ່າເກົ່າຍ້ອນວ່າຂະບວນການຜະລິດກ້າວຫນ້າ. ບັນຫານີ້ກາຍເປັນບັນຫາໂດຍສະເພາະໃນໄລຍະການຫຸ້ມຫໍ່ແລະການທົດສອບຕໍ່ໄປ, ບ່ອນທີ່ການເຫນັງຕີງຂອງອຸນຫະພູມແລະຄວາມກົດດັນກົນຈັກເພີ່ມເຕີມສາມາດເຮັດໃຫ້ microcracks ເຫຼົ່ານີ້ພັດທະນາໄປສູ່ການກະດູກຫັກທີ່ເຫັນໄດ້, ອາດຈະນໍາໄປສູ່ຄວາມລົ້ມເຫຼວຂອງຊິບ.
ເພື່ອຫຼຸດຜ່ອນຄວາມສ່ຽງນີ້, ມັນເປັນສິ່ງຈໍາເປັນທີ່ຈະຄວບຄຸມຂະບວນການຕັດຢ່າງລະມັດລະວັງໂດຍການເພີ່ມປະສິດທິພາບຕົວກໍານົດການເຊັ່ນຄວາມໄວຕັດ, ຄວາມກົດດັນແລະອຸນຫະພູມ. ການນໍາໃຊ້ວິທີການຕັດຮຸກຮານຫນ້ອຍ, ເຊັ່ນ laser dicing, ສາມາດຫຼຸດຜ່ອນຄວາມກົດດັນກົນຈັກກ່ຽວກັບ wafer ແລະຫຼຸດຜ່ອນການສ້າງຕັ້ງຂອງ microcracks ໄດ້. ນອກຈາກນັ້ນ, ການປະຕິບັດວິທີການກວດສອບແບບພິເສດເຊັ່ນການສະແກນອິນຟາເຣດ ຫຼືການຖ່າຍພາບ X-ray ໃນລະຫວ່າງຂະບວນການ wafer dicing ສາມາດຊ່ວຍກວດຫາຮອຍແຕກໃນຂັ້ນຕົ້ນເຫຼົ່ານີ້ກ່ອນທີ່ມັນຈະເຮັດໃຫ້ເກີດຄວາມເສຍຫາຍຕື່ມອີກ.
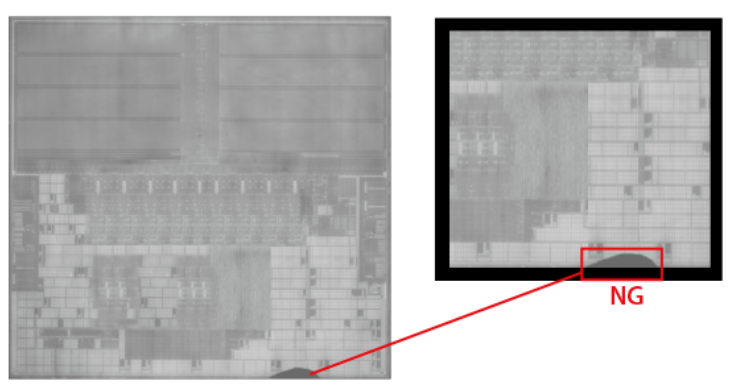
ຄວາມເສຍຫາຍຂອງຫນ້າດິນ wafer ແມ່ນຄວາມກັງວົນທີ່ສໍາຄັນໃນຂະບວນການ dicing, ຍ້ອນວ່າມັນສາມາດມີຜົນກະທົບໂດຍກົງຕໍ່ການປະຕິບັດແລະຄວາມຫນ້າເຊື່ອຖືຂອງ chip. ຄວາມເສຍຫາຍດັ່ງກ່າວສາມາດເກີດຈາກການນໍາໃຊ້ເຄື່ອງມືຕັດທີ່ບໍ່ເຫມາະສົມ, ຕົວກໍານົດການຕັດທີ່ບໍ່ຖືກຕ້ອງ, ຫຼືຄວາມບົກຜ່ອງດ້ານວັດສະດຸທີ່ມີຢູ່ໃນ wafer ຕົວມັນເອງ. ໂດຍບໍ່ສົນເລື່ອງຂອງສາເຫດ, ຄວາມເສຍຫາຍເຫຼົ່ານີ້ສາມາດນໍາໄປສູ່ການປ່ຽນແປງໃນຄວາມຕ້ານທານໄຟຟ້າຫຼື capacitance ຂອງວົງຈອນ, ຜົນກະທົບຕໍ່ການປະຕິບັດໂດຍລວມ.
ເພື່ອແກ້ໄຂບັນຫາເຫຼົ່ານີ້, ສອງຍຸດທະສາດທີ່ສໍາຄັນແມ່ນໄດ້ຖືກຄົ້ນຫາ:
1.Optimizing ເຄື່ອງມືຕັດແລະຕົວກໍານົດການ: ໂດຍການນໍາໃຊ້ແຜ່ນໃບຄ້າຍຄືແຫຼມ, ປັບຄວາມໄວການຕັດ, ແລະດັດແປງຄວາມເລິກຂອງການຕັດ, ຄວາມເຂັ້ມຂົ້ນຂອງຄວາມກົດດັນໃນລະຫວ່າງຂະບວນການຕັດສາມາດຫຼຸດລົງ, ດັ່ງນັ້ນການຫຼຸດຜ່ອນຄວາມອາດສາມາດຂອງຄວາມເສຍຫາຍ.
2.Exploring ເຕັກໂນໂລຊີການຕັດໃຫມ່: ເຕັກນິກຂັ້ນສູງເຊັ່ນການຕັດເລເຊີແລະການຕັດ plasma ສະເຫນີຄວາມແມ່ນຍໍາທີ່ປັບປຸງໃນຂະນະທີ່ອາດຈະຫຼຸດຜ່ອນລະດັບຄວາມເສຍຫາຍທີ່ເກີດຢູ່ໃນ wafer. ເທກໂນໂລຍີເຫຼົ່ານີ້ກໍາລັງຖືກສຶກສາເພື່ອຊອກຫາວິທີທີ່ຈະບັນລຸຄວາມຖືກຕ້ອງຂອງການຕັດສູງໃນຂະນະທີ່ຫຼຸດຜ່ອນຄວາມກົດດັນດ້ານຄວາມຮ້ອນແລະກົນຈັກໃນ wafer.
ພື້ນທີ່ຜົນກະທົບຄວາມຮ້ອນແລະຜົນກະທົບຂອງມັນຕໍ່ການປະຕິບັດ
ໃນຂະບວນການຕັດຄວາມຮ້ອນເຊັ່ນ: laser ແລະການຕັດ plasma, ອຸນຫະພູມສູງ inevitably ສ້າງເຂດຜົນກະທົບຄວາມຮ້ອນໃນຫນ້າດິນຂອງ wafer ໄດ້. ພື້ນທີ່ນີ້, ບ່ອນທີ່ gradient ອຸນຫະພູມມີຄວາມສໍາຄັນ, ສາມາດປ່ຽນແປງຄຸນສົມບັດຂອງວັດສະດຸ, ຜົນກະທົບຕໍ່ການປະຕິບັດສຸດທ້າຍຂອງຊິບ.
ຜົນກະທົບຂອງເຂດໄດ້ຮັບຜົນກະທົບຈາກຄວາມຮ້ອນ (TAZ):
ການປ່ຽນແປງໂຄງສ້າງ Crystal: ພາຍໃຕ້ອຸນຫະພູມສູງ, ປະລໍາມະນູພາຍໃນອຸປະກອນການ wafer ອາດຈະ rearrange, ເຊິ່ງກໍ່ໃຫ້ເກີດການບິດເບືອນຂອງໂຄງສ້າງໄປເຊຍກັນ. ການບິດເບືອນນີ້ເຮັດໃຫ້ວັດສະດຸອ່ອນເພຍ, ຫຼຸດຜ່ອນຄວາມເຂັ້ມແຂງກົນຈັກແລະຄວາມຫມັ້ນຄົງ, ເຊິ່ງເພີ່ມຄວາມສ່ຽງຂອງຄວາມລົ້ມເຫຼວຂອງຊິບໃນລະຫວ່າງການໃຊ້ງານ.
ການປ່ຽນແປງໃນຄຸນສົມບັດໄຟຟ້າ: ອຸນຫະພູມສູງສາມາດປ່ຽນແປງຄວາມເຂັ້ມຂົ້ນຂອງຜູ້ໃຫ້ບໍລິການແລະການເຄື່ອນໄຫວໃນວັດສະດຸ semiconductor, ຜົນກະທົບຕໍ່ການນໍາໄຟຟ້າຂອງຊິບແລະປະສິດທິພາບການສົ່ງໄຟຟ້າໃນປະຈຸບັນ. ການປ່ຽນແປງເຫຼົ່ານີ້ອາດຈະເຮັດໃຫ້ການປະຕິບັດຂອງຊິບຫຼຸດລົງ, ເຊິ່ງອາດຈະເຮັດໃຫ້ມັນບໍ່ເຫມາະສົມກັບຈຸດປະສົງທີ່ຕັ້ງໄວ້.
ເພື່ອຫຼຸດຜ່ອນຜົນກະທົບເຫຼົ່ານີ້, ການຄວບຄຸມອຸນຫະພູມໃນລະຫວ່າງການຕັດ, ການເພີ່ມປະສິດທິພາບຂອງຕົວກໍານົດການຕັດ, ແລະວິທີການຂຸດຄົ້ນເຊັ່ນເຄື່ອງເຮັດຄວາມເຢັນຫຼືການປິ່ນປົວຫຼັງການປຸງແຕ່ງແມ່ນຍຸດທະສາດທີ່ຈໍາເປັນເພື່ອຫຼຸດຜ່ອນຂອບເຂດຂອງຜົນກະທົບຄວາມຮ້ອນແລະຮັກສາຄວາມສົມບູນຂອງວັດສະດຸ.
ໂດຍລວມແລ້ວ, ທັງ microcracks ແລະເຂດຜົນກະທົບຄວາມຮ້ອນແມ່ນສິ່ງທ້າທາຍທີ່ສໍາຄັນໃນເຕັກໂນໂລຊີ wafer dicing. ສືບຕໍ່ຄົ້ນຄ້ວາ, ຄຽງຄູ່ກັບຄວາມກ້າວຫນ້າທາງດ້ານເຕັກໂນໂລຢີແລະມາດຕະການຄວບຄຸມຄຸນນະພາບ, ຈະມີຄວາມຈໍາເປັນເພື່ອປັບປຸງຄຸນນະພາບຂອງຜະລິດຕະພັນ semiconductor ແລະເສີມຂະຫຍາຍການແຂ່ງຂັນຕະຫຼາດຂອງພວກເຂົາ.
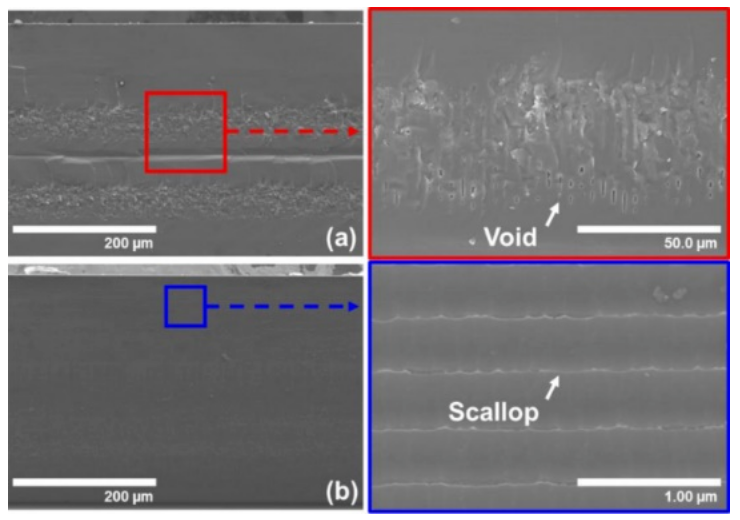
ມາດຕະການເພື່ອຄວບຄຸມເຂດຜົນກະທົບຄວາມຮ້ອນ:
ການເພີ່ມປະສິດທິພາບຕົວກໍານົດການຂະບວນການຕັດ: ການຫຼຸດຜ່ອນຄວາມໄວຕັດແລະພະລັງງານສາມາດຫຼຸດຜ່ອນຂະຫນາດຂອງເຂດຜົນກະທົບຄວາມຮ້ອນ (TAZ). ນີ້ຊ່ວຍໃນການຄວບຄຸມປະລິມານຄວາມຮ້ອນທີ່ຜະລິດໃນລະຫວ່າງຂະບວນການຕັດ, ເຊິ່ງມີຜົນກະທົບໂດຍກົງຕໍ່ຄຸນສົມບັດຂອງວັດສະດຸຂອງ wafer.
ເທັກໂນໂລຍີຄວາມເຢັນແບບພິເສດ: ການນຳໃຊ້ເທັກໂນໂລຍີເຊັ່ນ: ຄວາມເຢັນໄນໂຕຣເຈນຂອງແຫຼວ ແລະ ຄວາມເຢັນ microfluidic ສາມາດຈຳກັດຂອບເຂດຂອງເຂດຜົນກະທົບຄວາມຮ້ອນໄດ້ຢ່າງຫຼວງຫຼາຍ. ວິທີການເຮັດຄວາມເຢັນເຫຼົ່ານີ້ຊ່ວຍກະຈາຍຄວາມຮ້ອນໄດ້ມີປະສິດທິພາບຫຼາຍ, ດັ່ງນັ້ນຈຶ່ງຮັກສາຄຸນສົມບັດວັດສະດຸຂອງ wafer ແລະຫຼຸດຜ່ອນຄວາມເສຍຫາຍຈາກຄວາມຮ້ອນ.
ການຄັດເລືອກວັດສະດຸ: ນັກຄົ້ນຄວ້າກໍາລັງຂຸດຄົ້ນວັດສະດຸໃຫມ່, ເຊັ່ນ: ທໍ່ nanotubes ກາກບອນແລະ graphene, ທີ່ມີຄຸນສົມບັດຄວາມຮ້ອນທີ່ດີເລີດແລະຄວາມເຂັ້ມແຂງກົນຈັກ. ວັດສະດຸເຫຼົ່ານີ້ສາມາດຫຼຸດຜ່ອນເຂດຜົນກະທົບຄວາມຮ້ອນໃນຂະນະທີ່ປັບປຸງປະສິດທິພາບໂດຍລວມຂອງຊິບ.
ສະຫຼຸບແລ້ວ, ເຖິງແມ່ນວ່າເຂດຜົນກະທົບຄວາມຮ້ອນແມ່ນຜົນສະທ້ອນທີ່ບໍ່ສາມາດຫຼີກລ່ຽງໄດ້ຂອງເຕັກໂນໂລຢີການຕັດຄວາມຮ້ອນ, ມັນສາມາດຄວບຄຸມໄດ້ຢ່າງມີປະສິດທິພາບໂດຍຜ່ານເຕັກນິກການປຸງແຕ່ງທີ່ດີທີ່ສຸດແລະການຄັດເລືອກວັດສະດຸ. ການຄົ້ນຄວ້າໃນອະນາຄົດອາດຈະສຸມໃສ່ການປັບລະອຽດແລະຂະບວນການຕັດຄວາມຮ້ອນອັດຕະໂນມັດເພື່ອບັນລຸ dicing wafer ທີ່ມີປະສິດທິພາບແລະຊັດເຈນກວ່າ.

ຍຸດທະສາດການດຸ່ນດ່ຽງ:
ການບັນລຸຄວາມສົມດຸນທີ່ດີທີ່ສຸດລະຫວ່າງຜົນຜະລິດຂອງ wafer ແລະປະສິດທິພາບການຜະລິດແມ່ນສິ່ງທ້າທາຍຢ່າງຕໍ່ເນື່ອງໃນເຕັກໂນໂລຢີຂອງ wafer dicing. ຜູ້ຜະລິດຈໍາເປັນຕ້ອງພິຈາລະນາປັດໃຈຫຼາຍຢ່າງເຊັ່ນ: ຄວາມຕ້ອງການຂອງຕະຫຼາດ, ຄ່າໃຊ້ຈ່າຍໃນການຜະລິດ, ແລະຄຸນນະພາບຂອງຜະລິດຕະພັນ, ເພື່ອພັດທະນາຍຸດທະສາດການຜະລິດທີ່ສົມເຫດສົມຜົນແລະຕົວກໍານົດການຂະບວນການ. ໃນຂະນະດຽວກັນ, ແນະນໍາອຸປະກອນການຕັດທີ່ກ້າວຫນ້າ, ການປັບປຸງຄວາມສາມາດຂອງຜູ້ປະຕິບັດງານ, ແລະເສີມຂະຫຍາຍການຄວບຄຸມຄຸນນະພາບຂອງວັດຖຸດິບແມ່ນມີຄວາມຈໍາເປັນໃນການຮັກສາຫຼືແມ້ກະທັ້ງການປັບປຸງຜົນຜະລິດໃນຂະນະທີ່ເພີ່ມປະສິດທິພາບການຜະລິດ.
ສິ່ງທ້າທາຍ ແລະໂອກາດໃນອະນາຄົດ:
ດ້ວຍຄວາມກ້າວຫນ້າຂອງເທກໂນໂລຍີ semiconductor, ການຕັດ wafer ປະເຊີນກັບສິ່ງທ້າທາຍແລະໂອກາດໃຫມ່. ໃນຂະນະທີ່ຂະຫນາດຊິບຫຼຸດລົງແລະການລວມຕົວເພີ່ມຂຶ້ນ, ຄວາມຕ້ອງການຂອງການຕັດຄວາມຖືກຕ້ອງແລະຄຸນນະພາບເພີ່ມຂຶ້ນຢ່າງຫຼວງຫຼາຍ. ໃນເວລາດຽວກັນ, ເຕັກໂນໂລຢີທີ່ພົ້ນເດັ່ນຂື້ນໃຫ້ແນວຄວາມຄິດໃຫມ່ສໍາລັບການພັດທະນາເຕັກນິກການຕັດ wafer. ຜູ້ຜະລິດຕ້ອງຢູ່ກັບນະໂຍບາຍດ້ານຕະຫຼາດແລະທ່າອ່ຽງເຕັກໂນໂລຊີ, ການປັບປຸງແລະການປັບປຸງຍຸດທະສາດການຜະລິດແລະຕົວກໍານົດການຂະບວນການເພື່ອຕອບສະຫນອງການປ່ຽນແປງຂອງຕະຫຼາດແລະຄວາມຕ້ອງການເຕັກໂນໂລຊີ.
ສະຫລຸບລວມແລ້ວ, ໂດຍການລວມເອົາການພິຈາລະນາຄວາມຕ້ອງການຂອງຕະຫຼາດ, ຄ່າໃຊ້ຈ່າຍໃນການຜະລິດ, ແລະຄຸນນະພາບຂອງຜະລິດຕະພັນ, ແລະໂດຍການນໍາສະເຫນີອຸປະກອນແລະເຕັກໂນໂລຢີທີ່ກ້າວຫນ້າ, ການເພີ່ມທັກສະຂອງຜູ້ປະກອບການ, ແລະການສ້າງຄວາມເຂັ້ມແຂງການຄວບຄຸມວັດຖຸດິບ, ຜູ້ຜະລິດສາມາດບັນລຸຄວາມສົມດຸນທີ່ດີທີ່ສຸດລະຫວ່າງຜົນຜະລິດຂອງ wafer ແລະປະສິດທິພາບການຜະລິດໃນລະຫວ່າງການ dicing wafer, ນໍາໄປສູ່ການຜະລິດຜະລິດຕະພັນ semiconductor ທີ່ມີປະສິດທິພາບແລະມີຄຸນນະພາບສູງ.
ການຄາດຄະເນໃນອະນາຄົດ:
ດ້ວຍຄວາມກ້າວຫນ້າທາງດ້ານເຕັກໂນໂລຢີຢ່າງໄວວາ, ເຕັກໂນໂລຢີ semiconductor ມີຄວາມກ້າວຫນ້າໃນຈັງຫວະທີ່ບໍ່ເຄີຍມີມາກ່ອນ. ໃນຖານະເປັນບາດກ້າວທີ່ສໍາຄັນໃນການຜະລິດ semiconductor, ເຕັກໂນໂລຊີການຕັດ wafer ແມ່ນ poised ສໍາລັບການພັດທະນາໃຫມ່ທີ່ຫນ້າຕື່ນເຕັ້ນ. ເບິ່ງໄປຂ້າງຫນ້າ, ເຕັກໂນໂລຊີການຕັດ wafer ຄາດວ່າຈະບັນລຸການປັບປຸງທີ່ສໍາຄັນໃນຄວາມແມ່ນຍໍາ, ປະສິດທິພາບ, ແລະຄ່າໃຊ້ຈ່າຍ, ສັກຢາທີ່ສໍາຄັນໃຫມ່ເຂົ້າໄປໃນການຂະຫຍາຍຕົວຢ່າງຕໍ່ເນື່ອງຂອງອຸດສາຫະກໍາ semiconductor.
ເພີ່ມຄວາມຊັດເຈນ:
ໃນການສະແຫວງຫາຄວາມແມ່ນຍໍາທີ່ສູງຂຶ້ນ, ເຕັກໂນໂລຢີການຕັດ wafer ຈະສືບຕໍ່ຊຸກຍູ້ການຈໍາກັດຂອງຂະບວນການທີ່ມີຢູ່. ໂດຍການສຶກສາຢ່າງເລິກເຊິ່ງກົນໄກທາງກາຍະພາບແລະເຄມີຂອງຂະບວນການຕັດແລະການຄວບຄຸມຕົວກໍານົດການຕັດທີ່ຊັດເຈນ, ຜົນໄດ້ຮັບການຕັດລະອຽດຈະບັນລຸໄດ້ເພື່ອຕອບສະຫນອງຄວາມຕ້ອງການການອອກແບບວົງຈອນທີ່ສັບສົນຫຼາຍ. ນອກຈາກນັ້ນ, ການຂຸດຄົ້ນວັດສະດຸໃຫມ່ແລະວິທີການຕັດຈະປັບປຸງຜົນຜະລິດແລະຄຸນນະພາບຢ່າງຫຼວງຫຼາຍ.
ການເພີ່ມປະສິດທິພາບ:
ອຸປະກອນຕັດ wafer ໃຫມ່ຈະສຸມໃສ່ການອອກແບບທີ່ສະຫຼາດແລະອັດຕະໂນມັດ. ການນໍາສະເຫນີລະບົບການຄວບຄຸມຂັ້ນສູງແລະສູດການຄິດໄລ່ຈະຊ່ວຍໃຫ້ອຸປະກອນສາມາດປັບຕົວກໍານົດການຕັດອັດຕະໂນມັດເພື່ອຮອງຮັບວັດສະດຸທີ່ແຕກຕ່າງກັນແລະຄວາມຕ້ອງການການອອກແບບ, ດັ່ງນັ້ນການປັບປຸງປະສິດທິພາບການຜະລິດຢ່າງຫຼວງຫຼາຍ. ນະວັດຕະກໍາເຊັ່ນ: ເຕັກໂນໂລຊີການຕັດຫຼາຍ wafer ແລະລະບົບການປ່ຽນແຜ່ນໃບຢ່າງໄວວາຈະມີບົດບາດສໍາຄັນໃນການເພີ່ມປະສິດທິພາບ.
ການຫຼຸດຜ່ອນຄ່າໃຊ້ຈ່າຍ:
ການຫຼຸດຜ່ອນຄ່າໃຊ້ຈ່າຍແມ່ນທິດທາງທີ່ສໍາຄັນສໍາລັບການພັດທະນາເຕັກໂນໂລຢີການຕັດ wafer. ເນື່ອງຈາກວັດສະດຸໃຫມ່ແລະວິທີການຕັດໄດ້ຖືກພັດທະນາ, ຄ່າໃຊ້ຈ່າຍອຸປະກອນແລະຄ່າໃຊ້ຈ່າຍໃນການບໍາລຸງຮັກສາຄາດວ່າຈະສາມາດຄວບຄຸມໄດ້ຢ່າງມີປະສິດທິພາບ. ນອກຈາກນັ້ນ, ການເພີ່ມປະສິດທິພາບຂະບວນການຜະລິດແລະການຫຼຸດຜ່ອນອັດຕາການຂູດຂີ້ເຫຍື້ອຈະຫຼຸດລົງຕື່ມອີກໃນລະຫວ່າງການຜະລິດ, ເຊິ່ງເຮັດໃຫ້ຄ່າໃຊ້ຈ່າຍໃນການຜະລິດລວມຫຼຸດລົງ.
ການຜະລິດອັດສະລິຍະ ແລະ IoT:
ການເຊື່ອມໂຍງຂອງການຜະລິດທີ່ສະຫຼາດແລະເຕັກໂນໂລຢີອິນເຕີເນັດຂອງສິ່ງຕ່າງໆ (IoT) ຈະນໍາເອົາການປ່ຽນແປງທີ່ປ່ຽນແປງໄປສູ່ເຕັກໂນໂລຢີການຕັດ wafer. ໂດຍຜ່ານການເຊື່ອມຕໍ່ກັນແລະການແບ່ງປັນຂໍ້ມູນລະຫວ່າງອຸປະກອນ, ທຸກໆຂັ້ນຕອນຂອງຂະບວນການຜະລິດສາມາດຖືກກວດສອບແລະເພີ່ມປະສິດທິພາບໃນເວລາທີ່ແທ້ຈິງ. ນີ້ບໍ່ພຽງແຕ່ປັບປຸງປະສິດທິພາບການຜະລິດແລະຄຸນນະພາບຂອງຜະລິດຕະພັນ, ແຕ່ຍັງໃຫ້ບໍລິສັດທີ່ມີການຄາດຄະເນຕະຫຼາດທີ່ຖືກຕ້ອງຫຼາຍຂຶ້ນແລະສະຫນັບສະຫນູນການຕັດສິນໃຈ.
ໃນອະນາຄົດ, ເຕັກໂນໂລຊີການຕັດ wafer ຈະເຮັດໃຫ້ຄວາມກ້າວຫນ້າທີ່ໂດດເດັ່ນໃນຄວາມແມ່ນຍໍາ, ປະສິດທິພາບ, ແລະຄ່າໃຊ້ຈ່າຍ. ຄວາມກ້າວຫນ້າເຫຼົ່ານີ້ຈະຊຸກຍູ້ການພັດທະນາຢ່າງຕໍ່ເນື່ອງຂອງອຸດສາຫະກໍາ semiconductor ແລະນໍາເອົາການປະດິດສ້າງທາງດ້ານເຕັກໂນໂລຢີແລະຄວາມສະດວກສະບາຍຫຼາຍຂຶ້ນມາສູ່ສັງຄົມມະນຸດ.
ເວລາປະກາດ: 19-11-2024